Many supply chains are lengthy and dynamic and it’s impossible for managers to evaluate every action taken with detailed analysis. At Toyota they believe that reducing the lead time is the right thing to do. Managers there don’t spend time doing analysis every time they try to reduce lead time to prove that this is the correct thing to do. Instead they live by the guiding principle, confirmed over several decades, that reducing lead time eliminates waste, improves quality, and reduces costs.
Robert Martichenko and Kevin von Grabe, supply chain experts from LeanCor, have defined Eight Guiding Principles in their book Building A Lean Fulfillment Stream. These principles have proven essential in improving supply chains for years:
1. Eliminate all the waste in the fulfillment stream so that only value remains.
Creating flow in a fulfillment stream requires all departments and functions in an organization to work in harmony. Focusing on the fundamental lean principle of eliminating waste so that only value remains helps achieve this harmony.
2. Make customer consumption visible to all members of the fulfillment stream.
If customer consumption is visible across the entire fulfillment stream, then it is much easier for every participant to plan work based on the pull of customer demand.
3. Reduce lead time.
Reducing inbound and outbound logistics lead times will get orders to the customer faster. When a company can reduce lead times to the point where it can exceed leadtime expectations of the customer, it will no longer need to rely on forecasts and can “pull” material throughout the fulfillment stream. End-to-end fulfillment-stream lead times are reduced when overall inventory in the system is reduced.
4. Create level flow.
The ultimate goal is to have goods and information move in a predictable, consistent, and uninterrupted manner based on the actual demand of the customer. This is known as level flow. Level flow reduces variation in processes and tries to spread activities equally over working time. This minimizes the peaks and valleys in movement that create unevenness and overburden, which result in waste.
5. Use pull systems.
Use pull systems when level flow is not possible. A pull system is an inventoryreplenishment method (i.e., kanban) in which each downstream activity (customer consumption) signals its need to the next upstream activity. Pull systems reduce wasteful complexity in planning and overproduction that can occur with computerbased software programs such as material resource planning (MRP), and they permit visual control of the flow of materials in the fulfillment stream.
6. Increase velocity and reduce variation.
Velocity is the speed with which information and material move through the fulfillment stream. Meeting customer demand by delivering smaller shipments more frequently increases velocity. This helps to reduce inventories and lead times, which allows you to more easily adjust delivery to meet actual customer consumption.
7. Collaborate and use process discipline.
The collaboration of all participants in a fulfillment stream is necessary to identify problems in the stream, determine root causes, and develop appropriate countermeasures. To be truly effective, this collaboration must be combined with standard improvement processes and regular PDCA.
8. Focus on total cost of fulfillment.
Make decisions that will meet customer expectations at the lowest possible total cost —no matter where they occur in the fulfillment stream. This means eliminating decisions that benefit one part of the stream at the expense of others. This is the real challenge of building a lean fulfillment stream, but it can be achieved when all members share in the operational and financial benefits when waste is eliminated.
The Lean journey generally begins inside the four walls of the manufacturing facility, however eventually it extends to the supply base and customers. The eight guiding principles for turning your supply chain and logistics network into a smooth-flowing “fulfillment stream” delivers more value to customers while reducing the total cost of fulfillment. Implemented successfully, these principles prove convincingly that you can please customers and enjoy profitable growth from doing so.

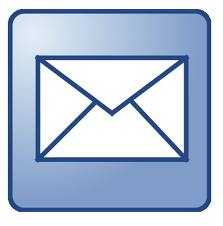





It is important to not only learn Lean protocols, but to implement them and use them everyday. These eight principles are very helpful for improving supply chains and the flow. Removing waste is an important part of Lean because by doing that, the system already becomes more efficient. Flow is also another important aspect because that can go hand in hand with reducing lead time. Focusing on improving the process and practicing Lean everyday will help any business or process thrive.
ReplyDeleteI got some valuable points through this blog.
ReplyDeleteWS-012T00: Windows Server 2019 Hybrid and Azure IaaS