Can Lean be represented by a single equation? In simple terms Lean can be defined as the most efficient use of resources in the creation of value for the end customer. Business is about the system or series of processes to satisfy the customer. Processes by definition can be defined. So if Lean is a business system for thinking customer value it can be represented below:
Demand is the amount of work in the system. Capacity is the resources available to do the work. Demand minus Capacity results in a Load on the system. If the demand is greater than the capacity the system is overloaded. If the demand is less than the capacity the system is considered underloaded.
John Seddon, author of Freedom from Command and Control
Taiichi Ohno, considered the father of the Toyota Production System, said that capacity is work plus waste. So if we identify and eliminate waste then "free" capacity is released into the system. Removing waste also allows for further reduction in failure demand.
Some underload is desirable because of variation in demand. A process that is loaded to 100% (where demand equals capacity) will frequently fail to meet the customer's requirements. When the system is underloaded then any spare resources should be directed to waste removal.
Reducing variation in demand by persuading customers to take smaller, more frequent batches can reduce the load on the system. This can result in improved customer service levels and the ability to handle more demand.
This Lean equation illustrates that reducing failure demand, reducing wastes, leveling the demand, reducing variation, and using slack capacity to focus on improving efficiency are all necessary for satisfying the customer's requirments. Furthermore, these activities result in feedback loops within your business system for continued input for PDCA (plan-do-check-act).

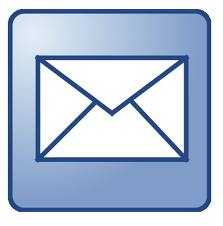





Hi Tim,
ReplyDeleteInteresting, but I'm wondering where the people fit into this equation...
Bryan
Bryan, you ask a good question. While I was looking at defining lean from a different angle where I did not specifically mention the people aspect. We know lean is 90% people and 10% tools. So for me the people make this equation happen. They recognize the relationship between demand and capacity. They build signals to react to changes. They work on adding value for the customer while eliminating waste. People interpret information from the system and thorugh PDCA solve problems with appropriate countermeasures. This system is dynamic and as such requires people to make it work.
ReplyDeleteHi Tim,
ReplyDeleteHow can I measure Demand Profile (failure Demand) and do not confuse the team about Process Quality???
Alexandra
Alexandra, failure demand is the scrap within the process that must be replaced or the failure from the field. This shows the importance to quality to any process. I guess it is a subset of process quality or yield. It is critical to look at defects and pareto of causes if you are going to improve your processes. You could look at first pass yield and return rate data. This may be different then how yield (typically a rolled throughput yield) is captured.
DeleteHi Tim,
ReplyDeleteYou have simplified lean for non-lean users, thank you for that. There is one just one question, how do you differentiate failure demand from non-value added?
Value Demand is the demand for service from customers, while Failure Demand is the demand caused by a failure to do something right for the customer. Failure demand is thus demand that only exists because initial demand was not satisfied properly.
DeleteFailure demand can also be defined as the delivery or production of products and services downstream as a result of defects in the system upstream.
Non-value added work is anything other than the absolute minimum resources of materials, machines, and manpower required to add value to the product.