The rule of thumb for minimizing movement is to begin with the largest motions first - the arms, legs, and torso - and then gradually focus on smaller and smaller types of motion - hands, wrists, fingers, and head. Hiroyuki Hirano
1. Start and stop manual operations using both hands in unison.
2. Keep arm motions simultaneous and symmetrical, the way you do when you are swimming - arms move in opposite directions with the same timing.
3. Minimize leg and torso motions. In assembly lines workers must often walk to the parts storage shelves and then back to the assembly area, or at the very least must twist to lift from a nearby cart or shelf, or reach to a shelf above the work area.
4. Use gravity instead of muscle power.
5. Avoid motions that zigzag or turn sharply.
6. Make motions rhythmical. Find a rhythm for your work that is easy to maintain over time.
7. Ensure good posture and easy, fluid motions. Bending over to work on a low table of straining to work on a surface that is too high for you will make your work harder and lead to other types of waste.
8. Use the feet, too; for instance, to operate foot switches to lift parts or move materials to and away from you.
9. Keep all necessary materials and tools close to you and in front of you.
10. Place materials and tools in their order of use. You can only do this if 5S is implemented and only a few parts are fed to your work area at a time.
11. Use inexpensive sources of power to feed materials through the operation.
12. Keep work tables and equipment at operator height.
13. Make the work environment comfortable.
14. Let the feet work for switching operations, keeping the hands free.
15. Minimize tool variety by integrating tool functions wherever possible.
16. All materials and parts should be easy to pick up, below chest level, and containers should be within easy reach.
17. All handles and knobs should be in convenient locations and in easy-to-grasp shapes. All handles and switches should be within easy reach without moving the torso.
This focus on body motion is not just about reducing cycle time and establishing production flow, though these are very important results of such improvement activities. Most people rejoice when they discover ways to eliminate the need to lift heavy items or overreach for tools and materials in order to do their jobs.

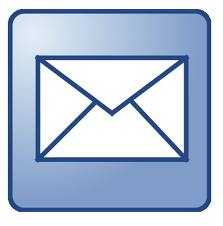





No comments:
Post a Comment