The goal of Meet-up is provide you an opportunity to meet some other influential voices in the Lean community. I will ask these authors a series of questions:
1. Who are you and what do you do?
My name is Kevin Meyer, and for the past seven years I have been president of Specialty Silicone Fabricators, a 400-person multi-site contract manufacturer of medical device components. After getting my chemical engineering degree from Rensselaer, I made light bulbs for Sylvania for several years, then medical products with Abbott for over a decade, telecom photonics for Newport, and started and sold my own contract manufacturing company.
On the side I run a lean knowledgebase, LeanCEO.com, and blog at Evolving Excellence. I’m a partner in Gemba Academy, which now provides online lean training to over 1,000 customers worldwide. I’m also a partner in another technology company outside of the lean space, and sit on the boards of two other tech companies.
Somehow I find the time to do some consulting, primarily focused on executive level lean leadership. I also consult with venture capital groups that need to understand the value in potential investment opportunities that include manufacturing operations. I’ve found VCs to be surprisingly open to non-traditional valuation methods.
With my wife Kim I live in Morro Bay, California, a small fishing village on the central coast, surrounded by over 220 wineries. For well over a decade I’ve succeeded at an annual goal to visit two new countries and learn something radically new each year.
2. How and when did you learn Lean?
My first experience with lean, although I didn’t know it yet, was with Sylvania in the mid-80s. We had just received our first contract to supply auto headlights to Toyota and had shipped over the first 100,000 units. A few weeks later we got a call that there was a major quality problem, and several folks went to Japan in response. On the Toyota conference table were five defective units. We discussed the problems, then asked for the rest of the defective units so we could analyze them. The Toyota folks looked at us funny then explained that those five were the defective units, and the quality level was unacceptable. We changed our underwear and flew home to a new reality.
In 1997, about seven years into my career with Abbott Laboratories, I was offered the opportunity to move to Salt Lake City to run the company’s largest molding facility. What they didn’t tell me was that this was a 24/7/365 operation, with every machine running, and they were still several weeks late delivering to multiple downstream assembly plants. So how do you catch up? The pressure was on.
I began to poke around at the early internet and discovered the Toyota Production System, lean, and The Association for Manufacturing Excellence. Thanks to the likes of Dave Hogg, Doc Hall, and Dan McDonnell I learned about several lean concepts, with quick changeover being the key to turning around our molding operation. Within six months we were caught up, and after a year we were actually getting rid of old, unnecessary equipment even though our demand continued to grow.
Since then I’ve been able to leverage lean to make significant improvements in many other operations. My knowledge of lean continues to grow thanks to knowing several people in the lean world, serving on the board of directors of AME for many years, visiting lean companies around the world, and especially by being able to try new ideas and concepts in the companies I’ve been part of.
3. How and why did you start blogging or writing about Lean?
As I was learning about lean in 1997 I began to capture a list of online resources on my computer. Colleagues at my company soon asked for that list, and then some colleagues outside of the company. I created Superfactory.com to hold those resources, which soon grew to become one of the largest lean resource sites. In 2004 I started the Evolving Excellence blog, and I continue to post a couple times a week. As I moved into more general management and executive roles I began to explore how lean could be applied to leadership – therefore I also shifted the Superfactory.com knowledgebase into LeanCEO.com, broadening the focus onto lean leadership.
Bill Waddell and I wrote Evolving Excellence – the book – in 2007. I am currently writing a book on how personal and professional leadership can be transformed by lean and zen principles. It’s a bit of a struggle as the unnecessary wordiness of most business texts, and the publishing business itself, flies in the face of the principles I’m promoting.
4. What does Lean mean to you?
I am definitely not a lean “purist” – I believe lean does and must evolve from the teachings of Woollard, Ford, Shingo, and Ohno. This puts me at odds with many in the lean community who argue vociferously whenever someone violates some principle apparently carved in stone and ensconced in Japan. Such argument is, ironically, a waste in itself.
My experience in the real world – running multiple manufacturing facilities and even companies – has taught me that every situation is unique even if the underlying issues have the same common roots. The core philosophy of lean – specifying and optimizing value from the perspective of the customer and leveraging people – remains relatively constant, as do the fundamental tools. But new ideas and new perspectives continue to present themselves. Just as lean teaches us to challenge perspectives and the status quo, philosophies and tools, including lean, should also always be challenged. And someday there will be something new.
5. What is the biggest myth or misconception of Lean?
Maybe it’s not the biggest myth or misconception, but not understanding or perhaps outright ignorance of the importance of the respect for people pillar of lean creates missed opportunities for most organizations on the lean journey. I believe it is also the reason for most lean failures.
Traditional financial statements account for the “cost” of people but there is no offsetting “value” – the value of experience, knowledge and creativity. This leads to crazy decisions like laying off thousands of experienced people to save a few bucks an hour on labor, while incurring supply chain, quality, and retraining costs.
By focusing on creating great people and using their ideas you can achieve incredible competitive advantage. My company successfully competes with companies in low labor “cost” countries like India and China – and we do it from what is supposedly one of the most business unfriendly states in the country. I can give you examples of many other companies doing the same, many of which are in low margin businesses. Stop complaining and start learning how to compete.
I’ve learned that the largest cost in business is not material, labor, or overhead – it’s unnecessary complexity. The key to reducing complexity is leveraging smart people who are given the right tools. I still haven’t seen a robot submit a suggestion for improvement – which is perhaps why some of the most efficient factories in the world have the lowest number of robots.
6. What is your current Lean passion, project, or initiative?
I have several ongoing lean projects, generally revolving around disseminating lean knowledge. Lean CEO continues to grow, as does Gemba Academy. I am also interested in how lean can be applied to unique industry niches, and with a couple partners am launching another startup in September to capitalize on one such opportunity.
However my strongest interest is with how lean and zen principles can dramatically transform both professional and personal leadership. The nexus is very interesting. Some of this grew out of necessity – having to juggle a bunch of projects as well as handle a difficult and chaotic family medical situation. But it also grew out of my occasional lean leadership consulting, which has almost always morphed into more of an executive coaching. Simplicity, clarity, enabling people, defined planning but living in the moment, hansei reflection.

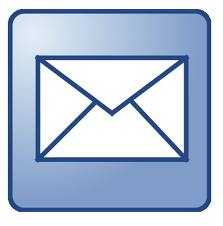





No comments:
Post a Comment