Who are you and what do you do?
I’m Karen Martin and I’m a business performance improvement consultant. I use that title rather than a Lean-specific title because I view Lean as a broad spectrum management philosophy, not merely an operations design strategy. However, I’m not entirely comfortable with “consultant” because I don’t operate as a traditional “I’ll-tell-you-what-to-do” consultant. I’m more of a facilitator, coach, and teacher than anything, but clients don’t often understand what that means. So, for familiarity, I stick with “consultant.”
I started my consulting practice in 1993 after I successfully built and managed operations in hospitals, clinical laboratories, and health insurers, a period during which I became enthralled with all-things-Deming.
As a consultant, I initially specialized in healthcare. Since diversifying in 2000, I’ve worked with clients in nearly every industry and at every stage of transformation. Engagements range from clients who are just beginning the Lean journey to those who are mature but want to deepen their understanding and accelerate results, re-invigorate their journey after stalling, or develop their leadership and/or internal improvement teams.
How and when did you learn Lean?
I guess you could say the late 80’s—if you consider Deming to be the forefather of Lean. I was introduced to “Lean” in 2000 when I took a brief hiatus from consulting to serve as the interim Director for San Diego State University’s Institute for Quality and Productivity. At that point, I had never stepped foot in a manufacturing setting. But as I sat through the Lean Manufacturing program that I was responsible for, I was instantly struck by how similar manufacturing and the service sector were—a connection that many struggle to see. And “you had me at Lean” is an understatement. Every fiber in my body knew that Lean was the powerful transformer that it has the potential to be and my mission in life became clear. I decided to dedicate my remaining career to helping others see what I saw and to reap the many benefits of adopting Lean business management practices in office, service, and knowledge work environments.
How and why did you start blogging or writing about Lean?
I began teaching at the university level when I was only 26 and have always enjoyed teaching, whether in person, virtually, or in written form. One of my strengths as a teacher is helping people convert theory into practical application and simplifying complex concepts. In terms of writing, I’ve always been drawn to it. I was our high school newspaper editor and won the journalism award. And, at one point while living in L.A. and being surrounded by screenwriters, I aspired to be a thriller writer. I have 1.5 completed novels under my belt. But writing fiction—especially thrillers—is very hard work and a tough sell. So I turned my proverbial pen to business and am deeply satisfied with that transition.
What does Lean mean to you?
To me, Lean is about doing more with less. Simplifying. Having unbridled respect for your “customer,” whether a paying customer, an internal customer or even a “customer” at home. It’s about innovating 24-7, seeking and telling the unvarnished truth, and seeing the world through a holistic lens. Seeing similarities before differences. Getting rid of anything that doesn’t matter and doesn’t add value. To Lean is a life philosophy, not merely a business management approach.
What is the biggest myth or misconception of Lean?
There are many. I guess the biggest one is that it’s about tools and process design versus what it really is—a method for managing one’s business from finance to operations, from HR to IT, from supply chain management to organizational design, from recruiting and onboarding to how meetings are run. Other misconceptions include a series of absolutes that aren’t always true, such as “batches are bad,” “all work should be standardized,” and “adding steps to a process is wrong.” And then there’s the one that drives me absolutely crazy: “Lean is about speed (or waste reduction) and Six Sigma is about quality.” Ah, no.
What is your current Lean passion, project, or initiative?
I’m currently in the throes of promoting my latest book, The Outstanding Organization, and am managing a full client load, one of which is a complete transformation. And I’m starting a new book with Productivity Press that I’ve been avoiding for years. It’s a how-to for creating value stream maps in the office/service sector, and I’m thrilled that Mike Osterling has agreed to co-author it with me. We really need a book on the subject out there and I gave up waiting for someone else to write it. My next hard cover “idea” book is also crystallizing. I plan to begin writing it in February. Life is good.

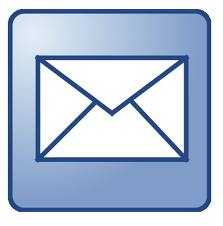





The best Lean Teacher ever! :)
ReplyDeleteI do enjoy what always Karen says.
Lean on!
Very nice article
ReplyDelete