![]() |
The 2010 BP Deepwater Horizon Oil Rig Explosion |
A
breakdown of quality is not an event. It is a process. Long before a quality
failure explodes on the front page of the paper, a company’s quality system has
been in trouble because of corporate decisions, policies and programs.
The
following are 15 tell-tale signs of eventual quality failure looming in your
business:
- Quality management efforts not
connected to competitive strategy or business results.
- Focus solely on cleaning up
messes rather than delivering superior products and customer service.
- Failure to spread responsibility
across the entire organization.
- Focusing on the external results
rather than the internal processes that produce them.
- Fragmented, partial approaches
yielding to "empowerment, without a clear strategy is chaos."
- Defining quality based on minimum
standards.
- Repetitive and recurring crisis
situations.
- The external quality message
doesn’t match internal practices.
- Failing to use a corrective
action process effectively to eliminate defects.
- An internal focus that is not
aimed at the customer.
- Performance measures that
reinforce quantity over quality.
- Assuming everyone knows what
“nonconforming” looks like.
- Thinking a common cause to
problems is operator error and relying on retraining as a corrective
action.
- Focus on speeding up the customer
response to issues instead of reducing the occurrence of issues.
- Quality management effort not
aligned within the company resulting in silos of execution.
Although
quality management practices have been implemented by many organizations all
over the world, such implementations have often failed. This failure rate is
largely attributed to the lack of integration between quality management
practices and business strategy.
In
a world of increased competitiveness and demanding customers who expect to have
the highest quality products at the lowest possible prices, quality is widely
recognized as a source of competitive advantage and is increasingly elevated to
strategic importance as an essential determinant of success. Hence, the
relationship between quality management and strategy is of great interest to practitioners.

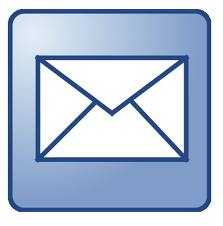





No comments:
Post a Comment