Click this link for A Lean Journey's Facebook Page Notes Feed.
Here is the next addition of tips from the Facebook page:
Lean
Tip #886 – Doing It Right Costs A Lot Less Than Doing It Over
Why
does it seem that there is never enough time to do it right, but always enough
time to do something over? If you want
to be a proactive organization it will pay huge dividends if everyone
concentrates on doing their job right the first time - even if it takes a
little longer to make sure it is right.
And by doing it right the first time, you not only increase your
company's efficiencies, but you can also have an immediate impact on customer
loyalty, retention and overall profits.
Lean
Tip #887 - Break The Daily Grind
Most
every employee is assigned a task according to his/her skill set; however, it
is important to consider rotating people throughout an organization. This will give them two things: One, a better
appreciation of what others do and two, it will help break the daily
complacency, monotony and boredom of a job.
You can do this by and giving people new tasks/job functions within the
company or other divisions -- which adds to their skill set and a better
overall view of the organization.
Lean
Tip #888 - Make it Easier to Get Things Done
After
removing distractions, you want to make working as easy as possible. In
general, make sure that tools for completing jobs are nearby the workers. Fewer
distractions will increase productivity.
Lean
Tip #889 – Don’t Work Hard, Work Smart
This
is somewhat of a cliché, but it has to be mentioned. We aspire to instill this
in all employees. On the long run this can make all the difference. Think about
this scenario, would you rather spend thirty minutes everyday on a specific
task, or implement a system that will require you to invest 2 hours for one day
then a couple of minutes every day instead of the thirty? I think the choice is
simple and this is an example of working smart.
Lean
Tip #890 - Offer Training to Build Employees Skills and Engage Them.
No
one wants to get stuck doing the same thing every day for the rest of their
lives. Encourage employees to take courses that expand their skill sets.
Imagine how much more productive your business will be when employees have
enhanced their ability to better communicate, solve problems, and find
improvements. Engaged employees are enthusiastic about their jobs, confident in
their ability to achieve excellence and motivated to have a greater impact on
the success of the business.
Lean
Tip #891 - Don’t Talk About It, Just Do It.
Lean
requires a bias for action. Just like the Nike tagline, you should go ahead and
just do it. Deploying Lean means you're following a PDCA (plan-do-check-act)
cycle and that it's okay to fail. Whether you succeed or fail, you're following
through on Lean.
Lean
Tip #892 - Discard Conventional Fixed Ideas.
Part
of problem solving is thinking outside of the box. Encourage people to think
this way and not in the same old way that got them into the problem to begin
with!
Lean
Tip #893 - We Don't Have Bad People, Just Bad Processes.
For
the most part, this is true. By concentrating on the process and building
continuous improvement there, you will have the culture change that you're
looking for.
Lean
Tip #894 - Do Not Seek Perfection. Do It Right Away.
Taiichi
Ohno used to regularly nag at people not to let a quality problem
"escape" to the next customer. You've got to stop what you're doing,
put a countermeasure on it and do it right away.
Lean
Tip #895 - Correct Mistakes Immediately.
You've
got to fix mistakes immediately. Don't wait for the next shift to do it. Don't
wait for the weekend to do it. Don't wait for maintenance to do it. Quality
depends on immediate action to correct mistakes.
Lean
Tip #896 - Do Not Spend Money For Kaizen.
It
is not necessary to spend money to fix every problem. All that proves is that
you have a lot of money. I don't care whether you're in manufacturing or health
care, you don't have "extra" money. Toyota says that they use their
wits, not their wallets, for continuous improvement.
Lean
Tip #897 - Question Everything. Ask "Why" Five Times.
A
brilliantly simple root cause problem-solving tool, asking why five times
becomes easier the more you do it. Adopting this as a default way of looking at
things will aid, not only your problem solving, but other areas, too.
Lean
Tip #898 - Ideas are Infinite. Execution is the Key.
This
simple maxim is often overlooked as people get caught up in meetings and so on.
You've got to be the change you want to see, not the change you'd like to see.
It's the same as not confusing better with best. You want to move to better
right away, not take forever working out what "best" looks like.
Lean
Tip #899 - Take No Action and Nothing Will Happen.
If
you do nothing, nothing changes. Be aware of items that stall your action. It's
better to have a 50-percent reduction in waste right away than it is to take no
action and hope for a 100-percent reduction in waste sometime in the future.

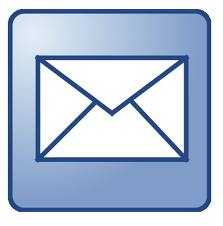





No comments:
Post a Comment