Click this link for A Lean Journey's Facebook Page Notes Feed.
Here is the next addition of tips from the Facebook page:
Lean
Tip #1111 – Respect: Speak Calmly and Listen to Others.
Respect
must always be a mutual concept, as you cannot hope to gain it without offering
it in the first instance. It is therefore crucial that you remain a good
listener at all times, and take the opinions of others on board before taking a
direct action or decision. On a similar note, you must always speak calmly when
interacting with both colleagues and superiors, as otherwise you run the risk
of alienating them and developing a reputation as someone who is difficult to
work with.
Lean
Tip #1112 – Respect: Go Above and Beyond the Call of Duty.
Whenever
you start a job, you are given a basic salary and a job description that
outlines the tasks under your control. As you develop relationships with those
around you and earn greater levels of responsibility, however, you must be
willing to operate outside of these boundaries and do more than is expected of
you. Whether this is covering for an unforeseen absence or completing a project
within a specified deadline, your willingness to go above and beyond the call
of duty will ensure that you remain well-respected among your peers.
Lean
Tip #1113 – Respect: Make Collaboration a Key Aspect of Your Work Life.
There
will be instances where it is necessary to work on a collaborative project with
different colleagues and departments. This can be challenging, especially if
you are unfamiliar with their working methods or prefer to operate on an
independent basis. Earning universal respect requires you to communicate with
people across multiple levels, regardless of status or pre-existing
relationship. With this in mind, you must always be open to collaboration and
strive to work effectively with any kind of team.
Lean
Tip #1114 – Respect: Practice the Virtue of Patience.
Professional
respect relies on your ability to showcase both compassion and understanding,
as you must make the most of your colleagues’ strengths while also making
allowances for their weaknesses. Everyone brings a unique skill-set to the
workplace, while each individual also works at his or her own pace. It is
crucial that you are patient when dealing with colleagues and superiors, as
this enables you to become a productive and respected member of a multi-layered
organization.
Lean
Tip #1115 – Respect: Become a Problem Solver.
Professional
respect can be achieved simply by adding unique value to the workplace. While
you can do this by undertaking your role tenaciously and effectively, it is
also possible to become a talented problem solver with skills in analytical
thinking, strategizing, and negotiation. Every workplace needs proactive
problem solvers, so by taking on the mantle and fulfilling this need you can
gain newfound respect among your colleagues.
Lean
Tip #1116 – Teamwork: Make Every Team Member Feel Valued
Success
as a team can only come when each team member is aware of the importance of
their role in the team’s success. Involve all team members by sharing any
available information relevant to the goal/project and any deadlines. Assign
them with responsibility for specific goals/outcomes and reward all members of
the team for achieving them.
Lean
Tip #1117 – Teamwork: Set Increasingly Challenging Team-Based Goals
Each
time the team reaches a goal, set a more challenging goal for them to achieve
to encourage team members to stretch themselves and learn from and build on
their previous successes. Recognize the team for meeting the challenge and
openly discuss how their team effort led their achieving the goal.
Lean
Tip #1118 – Teamwork: Incorporate Team-Based Problem Solving into Staff Meetings
At
each team meeting ask every team member to share a project or task they might
feel stuck on, or challenged by, and request that other team members give feedback,
provide some mentoring and share their ideas to help resolve the dilemma or
impasse. Encourage team brainstorming of solutions.
Lean
Tip #1119 – Teamwork: Discuss Team Dynamics on a Regular Basis
Encourage
open communication in team meetings about the team dynamic - for example, talk
specifically about what’s working well and what could work better. Use this as
an opportunity for team members to discuss how they can work more effectively
as a team, but never to whinge or criticize one another in front of other team
members. Also encourage conversations reflecting on what has enabled positive
achievements as a team.
Lean
Tip #1120 – Teamwork: Act as a Guide
Every
team needs a great leader who’s willing to guide the team in working and making
decisions collaboratively. The team leader must also be committed to reaching
the team’s goals and have strong communication skills to be able to share their
passion and vision for success.
Lean
Tip #1121 - Set Workers Up For Success
Workers who are comfortable in their workspace
are more likely to be successful and productive than those who feel
uncomfortable. Factors that come into play in worker comfort include
cleanliness, accessibility, safety, and ease of use of working environments.
Lean Tip # 1122 - Be Consistent and Continually
Reassess
Continuous
improvement is one of the main tenets of lean manufacturing, and with good
reason. Ensure
that workers at all levels are invested in the lean manufacturing process and
are accountable for maintaining the environment is crucial. In addition, you
will need to adapt and change things along the way. Be sure to stay on top of
how efficient the workflow is, how well practices are being implemented, and
determine whether changes need to be made.
Lean
Tip #1123 - All Employees Should Contribute to Lean
Lean
should be practiced by employees at all levels and in all departments at your
company. By engaging people in the process of problem-solving, it reduces
resistance to the recommended solutions. Rather, participants want to see their
ideas implemented and be successful because they are their ideas.
Lean
Tip #1124 - Eliminate Scrap
People
don’t always understand the true cost when it comes to scrap. If you make a
product that must be thrown away, you don’t just lose the materials. You also
lose the labor and the opportunity for profit. Even if you can rework a
product, you’re still losing out on the labor and cutting into your profit.
Lean
Tip #1125 - Ask for Help
You
can ask people for advice on what to do and what they did in similar situations
like yours. But you can also ask for more practical help. You don´t have to
solve every problem on your own and sometimes it feels better to have someone
by your side, even if it is just for emotional support.

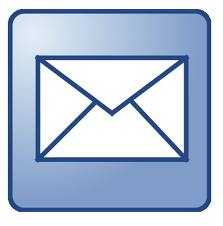





No comments:
Post a Comment