![]() |
www.kaizenworld.com |
Many
consultants will advise clients that 5S is a good place to start when starting
your Lean journey. This is for good
reason. 5S is a process and method for
creating and maintaining an organized, clean, and high performance
workplace. It enables anyone to
distinguish between normal and abnormal conditions at a glance. 5S can be the foundation for continuous
improvement, zero defects, cost reductions and a more productive work
space. The 5S methodology is a
systematic way to improve the workplace, processes and products through
employee involvement.
Embarking on
your Lean journey with implementing 5S is beneficial for several reasons:
1. Organized
and safe work place. With some simple training, supplies, time and a little bit
of elbow grease, you can carve out a very well organized area in your
workplace. People are less likely to get
injured in an organized environment.
2. Provides
structure and discipline. Successful
implementation of 5S requires that processes be defined and process ownership
assigned. This begins to create basic process team structures with assigned
responsibility and accountability for process conditions and performance.
3. Creates
visibility. It allows you to see problems more easily. If you have a good 5S
condition, problems can be seen easily. When
process conditions start to become standardized, leading to the surfacing of
abnormal conditions, which in turn can lead to problem solving, learning, and
developing corrective and preventive actions.
4. Improves
morale. People enjoy
working in an organized environment.
Yes, there are those out there who really don’t mind working in a dirty,
filthy place, but studies have shown that morale is higher in companies with a
higher level of 5S.
5. Continuous
improvement. 5S begins to stimulate employee contributions and ideas for
improvement. It is important for firms that begin their improvement journey
with 5S to nurture the employee contributions which can flow out from 5S
activity.
5S is a
prerequisite for most other Lean tools. Well-implemented,
5S can open up entry points into flow and pull, equipment reliability,
standardized work, and value analysis. We know that Standard Work is a baseline
for all improvements, but if the workplace is unorganized and the necessary
items needed to do the job are not easy to locate, how can Standard Work be
followed? Without Standard Work, you
really don’t have a chance to improve the process and 5S is a critical
prerequisite.
So by starting
with something as simple as sorting through your items, setting them in a
designated space, shining them up, you can achieve higher levels of Safety,
Quality, Problem Solving and Morale. Not
to mention, you won’t really be able to proceed further in legitimately
implementing Lean practices. Don’t you
think that it’s worth it to rank 5S as a high priority for your workplace? Just make sure you are aware of the
commitment level you need to Standardize the practice and Sustain it, otherwise
all you are doing is “cleaning up” once in a while.

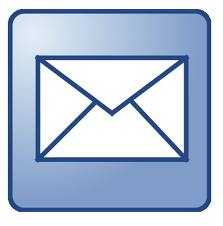





Cultural transformation in a company to Lean thinking/focus is where to start. Why? Lean is a new way of doing business. Slapping in tools, like 5S, and not changing the culture won't work. Slapping in tools like 5S is a Lean façade.
ReplyDeleteI don´t think tht the article is saying that. The way I understand it and how I teach it, is the fact, that if CIP and 5S will not be accepted and work, you definitely can forget any LEAN SYSTEM. And sure, before somebody starts with any tool, there needs to be a general commitment to walk that route....forever!
Delete5S is not the only place you can start a Lean Journey but as Gerhard says if you can't do this foundation element well then other elements of a Lean System will be challenging. You have to start with tools to transform the culture so people can see value and success from the new approach. You can't change people's minds without showing them what it looks like, why it is necessary, and how to do it.
Delete