Click this link for A Lean Journey's Facebook Page Notes Feed.
Here is the next addition of tips from the Facebook page:
Lean
Tip #1471 - Focus on the Rate of Production, or Takt Time.
This
is a heartbeat measurement for the team. One-piece flow is ideal, but any flow
is better than no flow. Pull at the demand of the customer, if possible. Then,
pull the material through the process rather than push it along. This may take
time. Setting up small work-in-process (WIP) or finished goods inventory (FGI)
locations from which teams can pull material through production can be a good
place to start. Holding areas also are known as Kanban areas, or supermarkets.
Lean
Tip #1472 - Create a Model Line.
Develop
a showplace within your shop where everyone can see how it should be done.
Start small, but don't pick a project that has no challenges. Develop key
measurements before and after the production line so that people can watch the
progress of your get-lean initiative. Finally, create a future-state map that
acts as your ideal value stream.
Lean
Tip #1473 - Don't Wait Until All the Stars Align Before You Begin.
There
is never an ideal time to start redoing your manufacturing process. There
always are reasons you should wait or gather more data, but a ready-fire-aim
approach is not all bad if it is applied to smaller aspects of the project.
Lean
Tip #1474 - Develop the Ability to Make “Every Part Every Day”
Develop
the ability to make “every part every day” (than every shift, than every hour
or pallet or pitch) in fabrication processes upstream of the pacemaker process.
By shortening changeover times and running smaller batches in you upstream
fabrication processes, those processes will be able to respond to changing
downstream needs more quickly. In turn
they will require even less inventory to be held in their supermarkets. This
applies to both discrete-parts manufacturing and process industries.
An
initial goal at many plants is to make at least “every part every day” for
high-running part numbers.
Lean
Tip #1475 - Use Kaizens to Teach and Make Rapid Changes
Use
a talented and experienced facilitator who has a deep understanding of Lean
tools and philosophy but keep training focused on a specific problem. This
helps to keep the training relevant to real world situations and ensures that
there are tangible outcomes from training activity. The kaizen might have an
objective to reduce setup time, reduce waiting time, or increase workplace
organization, for instance.
Lean
Tip #1476 - Benchmark with other companies
Visit
other companies that have successfully implemented lean to get ideas and
understanding; other companies are often delighted to present their lean
implementation progress. Networking is key to ensure global understanding with
other companies implementing Lean.
Lean
Tip #1477 - Set up a Lean Enterprise Steering Team
This
team would be responsible to provide support in the planning, resourcing,
implementation, and follow-up accountability for implementation. The steering
team is often identical to the normal line management team. The internal
resources and external consultants would provide consulting support to the
team. This infrastructure would resolve inter-departmental issues.
Lean
Tip #1478 - Leaders Must Thoroughly Understand, Believe In, and Live Lean
All
leaders must understand the work in detail and know how to involve people. If
the top is not driving the transformation, it will not happen. Then, to keep
the results sustainable you must have a system for both result- based and
process based performance measurement including measures for velocity of the
overall business process and the individual business processes.
Lean
Tip #1479 - Create a Positive Atmosphere
Be
tolerant towards mistakes committed in lean environment with a supportive and
learning attitude. Have patience with progress as this will be key to get
results and also try to create a blame free supportive environment. Have
courage to take risks at crucial stages to push things and resources to meet
the plan and achieve results.
Lean
Tip #1480 - Make Lean Mandatory
If
a company looks at Lean transformation as a "nice to do" in spare
time or as a voluntary activity, it will simply not happen. It needs to be
mandatory and people need to be given the space to think about improvements
they can make.
Lean
Tip #1481 - Involve Employees in the Change Process.
Employees
are not so much against change as they are against being changed. Any time
managers are going to implement organizational change, there is always a lag
between the time the change has been discussed at the management level and the
time the change is going to be implemented. Managers like to play like an
ostrich and believe that they are the only ones who know about the changes that
are going to take place. Unfortunately, while their heads are stuck in the sand
believing that no one else knows, employees are effectively undermining the
future changes with negative informal communication…the company grapevine. The
sooner you involve employees in the process, the better off you will be
implementing the change. A formal communication channel is more effective at
implementing change than a negative informal one.
Lean
Tip #1482 - Ask Employees For Commitment to Change.
Once
change has been announced, it is important that you personally ask for each
employee’s commitment to successfully implement the change. It is also
important that you assure the employee that if there are problems, you want to
hear about them. If a negative employee does not tell you, they will tell other
employees why the change will not work.
Lean
Tip #1483 - Expand and Improve Communication to Employees.
The
change process usually means that normal communication channels need to be improved.
First, give employees an opportunity to give you input. Start by becoming more
available and asking more questions. Get employees’ opinions and reactions to
the changes. Maintain your visibility and make it clear that you are an
accessible boss. More importantly, be a careful listener. Second, keep
employees updated on a regular basis. Just letting your employees know that you
have no new information is meaningful information to them. Strive to be
specific; clear up rumors and misinformation that clutter the communication
channels. Remember, it is almost impossible to over communicate.
Lean
Tip #1484 – Management Should Keep a Positive Attitude.
Your
attitude as a manager or supervisor will be a major factor in determining what
type of climate is exhibited by your employees. Your attitude is the one thing
that keeps you in control. Change can be stressful and confusing. Try to remain
upbeat, positive, and enthusiastic. Foster motivation in others. During times
of transition and change, try to compensate your employees for their extra
effort. Write a brief note of encouragement on their paychecks; leave an
affirming message on their voice mail; take them aside and tell them what a
great job they are doing; listen to their comments and suggestions. Last, try
to instill organizational change as a personal challenge that everyone can
meet…with success!
Lean
Tip #1485 - Raise Levels of Expectations.
Now
more than ever, you should ask more from your employees. It is expected that
more work needs to be done during the change process. While it may be most
practical to expect less in terms of performance, raise your levels of
expectations and theirs. During change, employees are more likely to alter
their work habits, so reach for the opportunity and push them to try harder and
work smarter. Require performance improvements and make the process
challenging, but remember to keep goals realistic in order to eliminate
frustration and failure.

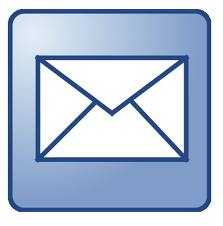




No comments:
Post a Comment