Last week I was able to join GBMP’s 12th Annual Northeast Lean Conference in Worcester, MA. The theme was on the tacit nature of implementing Lean, the importance of tying together the technical and social sides of Lean, the significance of management’s involvement and the ability of organizations to sustain the gains.
I thought I would share a few highlights from this year's conference.
The first presenter was Art Byrne who was instrumental in the Lean transformation at the company where I work. Art has transformed many businesses over his career and shared his formula which he described in he book Lean Turnaround. He found Lean was a strategy to run a business focusing on eliminating waste to deliver more customer value. A key element in his approach was Kaizen which is still done today at Wiremold (25 years later). Kaizen is powerful because it is key training vehicle to teach new thinking and gets everyone on board. Art explained the importance of moving from batch to flow production (where you work to takt time, 1 piece at a time, using standard work, via the pull of customer demand). I really liked his comment to all these black belts today: "
We are running a company not a karate class."
Another great speaker was Eric Dickson, CEO of UMass Healthcare, who shared a power message on strategy and Lean transformation. He claims many organizations spend very little time on the things that will really transform their business (ie. Strategy). Their are 5 points of emphasis in his approach:
1) Establish a pre-defined goal and then run experiments (kaizen)
2) Let the people doing work do experiments
3) Standard work leads to improvement
4) Transparency creates the necessary tension for improvement (share metrics and plans)
4) Framework for Performance excellence (how the management system is executed)
With the back drop of saving lives (healthcare) he shared a compelling vision for all.
LEI's John Shook shared the Lean Transformation Framework they use when working with companies, divisions, and individuals. Practice does not make perfect it makes permanent. Perfect practice can make perfect permanent. Deliberate practice explains a substantial amount of performance variance. We need to design the entire work experience that individuals experience. The framework consists:
1. Purpose – align around the problem to solve
2. Designing, doing and improving the work
3. Develop capability, develop people
4. Management system – leader behavior
5. Basic Thinking
Here is a video describing LEI's Lean Transformation Framework.
Here is a video describing LEI's Lean Transformation Framework.
• Leadership delegates change
• Middle management is not onboard
• Lack of shared vision
• Unrealistic expectations/little patience/time is not allocated
• Key systems that drive the right behavior are not in place
Mike took a look at the top 3 Lean models: 1) Shingo 2) Toyota Way 4P 3) LEI transformation model
to see how they compare. All have in common:
• Foundation of culture, long term vision and value mindset
• Focus on continous process improvements
• Respect for people and development of capabilities
• Continuous learning through structured problem solving, reflection, and kaizen
This suggests a pathway to Lean that all can use to transform their company.
There were many more great breakout sessions and lots of opportunity to network and connect with many great Lean thinkers and implementers alike. This is one of my favorite conferences.
Next year's conference will be held September 19-20, 2017 in Worcester, MA. The theme is on the integration of tools and culture. Mark your calendar so you don't miss out on a great opportunity.

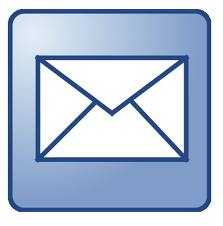





No comments:
Post a Comment