Click this link for A Lean Journey's Facebook Page Notes Feed.
Here is the next addition of tips from the Facebook page:
Lean
Tip #1531 – Create a Learning Organization By Promoting From Within
Employees
who have successfully learned new skills and abilities should be recognized and
encourage others to follow suit. One of the advantages of training is having
employees who are ready for a bigger role. Announce an internal job posting to
encourage employees to gain knowledge.
Lean
Tip #1532 - Develop Knowledge and Information Sharing into a Formal Process.
For a learning culture to be ingrained, it should be mandatory for all
individuals in the organization. Training and development plans that are not
formalized run the risk of not being taken seriously and as a result, not
implemented. People will be more encouraged to share knowledge and information
if they are required to do so. Formalizing the process makes sure that everyone
who needs the information gets it.
Lean
Tip #1533 - Drive People to Learn by Doing.
Training
is a way to impart knowledge. Learning is also about sharing lessons, telling
stories, doing, making mistakes and improving constantly. People learn the most
when they implement their knowledge to generate meaningful business results. Allow
people to make mistakes (and learn from them). People never experiment if they
have to pay a price for trying new things out.
Lean
Tip #1534 - Include all Employees in Learning Opportunities
For
a culture of learning to take root and grow, learning and development
opportunities must be inclusive. You can’t expect to build a culture of
learning unless learning opportunities reach every employee. This requires
managers and team leaders to be inclusive when selecting employees to
participate in learning and development activities. Give consideration to
employees throughout the entire organization – include staff at all levels, in
all departments and across all locations.
Each
person is unique, and people tend to learn in different ways. A
one-size-fits-all approach seldom works when it comes to learning and
development. It’s best to ensure learning opportunities are available to all
employees regardless of the special considerations. Flexibility goes a long way
when it comes to teaching employees across a large and dynamic workplace.
Lean
Tip #1535 - Create an “Employee-First” Culture
Steady,
long-term competitiveness requires an organization to be committed to putting
employees first and developing quality training programs that are linked to its
strategic objectives. Without a true commitment to the employees at all levels
throughout an organization, the journey to enhance organizational performance
will be an elusive adventure. Quality employees equate to organizational
success. Unqualified and poorly trained employees equate to organizational
failure.
Lean
Tip #1536 - Have a Strong Lean Improvement Strategy
You'll
need a solid plan and some attainable targets before implementing Lean. Utilize
checklists and to-do lists, and you’ll always be working towards a goal. Look
at every step in your process from the customer’s perspective: Is all that
you’re doing something that he or she would be willing to pay for? If not, it
is time to get back to the drawing board.
Lean
Tip #1537 – Bench Mark Other Lean Companies
Sometimes
we learn best by first witnessing the success of others. See the benefits of
lean in action. It is not difficult to find organizations that will allow you
to see their lean implementations (referred to as the Gemba walk). Take
detailed notes of what is highly effective in their Lean implementations, ask
questions, and get as much valuable information as you can in order to help you
formulate you own Lean strategy for implementation.
Lean
Tip #1538 - Get the Whole Team on Board
To
get the greatest advantages out of Lean, the entire organization should adopt
and promote its practices, and extend its influence to suppliers as well. You
must involve the people who are the closest to the work and you must get
support from senior management as well.
Lean
Tip #1539 - Discard Conventional Ideas
Part
of problem solving is thinking “outside of the box.” Encourage fresh
perspectives and ingenuity in your team in order to develop innovative ways to
forward Lean manufacturing without changing what is already efficient and
successful. With such a rapidly evolving climate in manufacturing, sometimes
conventional thought is what leads to the problem in the first place!
Lean
Tip #1540 - Don’t Just Talk About it, Do it!
Once
you have a Lean strategy in place, put it into fast and thorough action.
Naturally, implementation is what ultimately yields results and improvement.
The last think you want is to devise and formulate a Lean campaign that then
sits on the shelf and collects dust. Run with your Lean plans as soon as you
have everything nailed down.
Lean
Tip #1541 - Concentrate on bad processes, not people
By
concentrating on the processes and building continuous improvement, you will
have the culture change that you are looking for. Also, correct mistakes
immediately. Don’t wait for the next shift, the weekend or maintenance to do
it.
Lean
Tip #1542 – Make Kaizen a Strategic Objective
Link
kaizen methodologies, the process of continuous process improvements, to
strategic objectives. Execute kaizen events are monthly to drive performance.
Associates are involved and challenged. Resources are dedicated, and the
company is utilizing a strong continuous improvement office.
Lean
Tip #1543 - Educate Your Leaders in Lean Thinking
Start
at the top and educate your executives on the differences and benefits of
coaching versus counseling. Interview them on their perspectives on coaching
and assess their willingness to participate and support a coaching initiative.
Explain the benefits of coaching and ask them where they see applications for
coaching inside their organizations.
Lean
Tip #1544 – Plan Periodic Team Reflection
Perform
periodic reflection with the team in a manner that allows them to drive the
conversation. This will teach the team members reflection skills and will allow
you as a manager to get a full picture of the progress. Additionally, this can drive best practices
for future teams.
Lean
Tip #1545 - Give your Team the Proper Amount of Autonomy.
Teams
are often most efficient when they are self-managed. We want our teams to have
the freedom to work through their problems without being micromanaged as this
will encourage growth for natural leaders and create a sense of empowerment for
the team.

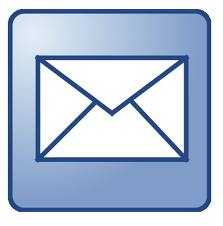




Focusing on bad processes rather than people is a smart approach that makes a real difference. Great tips!
ReplyDelete