Click this link for A Lean Journey's Facebook Page Notes Feed.
Here is the next addition of tips from the Facebook page:
Lean
Tip #1546 - Learn by Doing First and Training Second
The
Toyota Way is about learning by doing. I believe that in the early stages of
lean transformation there should be at least 80% doing and 20% training and
informing. The best training is training followed by immediately doing … or
doing followed by immediate training. The Toyota approach to training is to put
people in difficult situations and let them solve their way out of the
problems.
Lean
Tip #1547 - Use Kaizen to Teach and Make Rapid Change
Kaizen
frees up a cross-functional team to make changes quickly that otherwise can
drag on for months. Selecting the right people for the team is critical, as is
setting aside the time for those individuals and giving them a lot of
management support. Using a talented and experienced facilitator who has a deep
understanding of lean tools and philosophy with a specific problem to tackle
makes all the difference in what you can accomplish.
Lean
Tip #1548 - Use Value Stream Mapping to Develop Future State Visions
Value
stream mapping is a method for clearly showing in diagram form the material and
information flow. When developing the current state map, future state map, and
action plan for implementation, I always recommend using a cross-functional
group consisting of managers who can authorize resources and doers who are part
of the process being mapped. Mapping creates a language and tool for the team
to actually pick apart a specific process, see the waste, develop a lean
vision, and apply it to that particular process.
Lean
Tip #1549 – Organize Around Value Streams
In
most organizations, management is organized by process or function. In a
factory, there is a manager of the paint department, a manager of the assembly
department, and a manager of the maintenance department. In Lean Thinking,
Womack and Jones recommend creating value stream managers who have complete
responsibility for the value stream and can answer to the customer.
Lean
Tip #1550 - Realign Metrics with a Value Stream Perspective
“You
get what you measure” has become a truism in most companies. But metrics are
used very differently by Toyota compared to most companies. They are an overall
tool for tracking progress of the company and they are a key tool for
continuous improvement. At most companies they are mainly a tool for short-term
cost control by managers who do not understand what they are managing.
The
first step therefore is to eliminate non-lean metrics that are wreaking havoc
with those seriously invested in improving operational excellence. The next
step is to measure a variety of value stream metrics from lead time to
inventory levels to first-pass quality and treat these metrics as seriously as
labor productivity and other short-term cost metrics.
Lean
Tip #1551 - Figure Out How the Work Gets Done.
We
have lots of assumptions about how work gets done that don’t mirror exactly
what happens. After all, during the day-to-day grind, we don’t think about how
we do the work, we often just do it. Ask an outside observer to record the
steps of the process in a way that he/she could repeat it themselves if they
had to, without assistance.
Lean
Tip #1552 - Remove Inefficiencies and Waste.
Once
you know what the workflow of your process looks like, take a second look at
any step in the process that doesn’t directly create value for the customer.
Manage, improve, and smooth your process flow to eliminate non-valued-added
activity (e.g., wasted time, wasted movement, wasted inventory due to
overproduction, customer delays, waiting for approvals, delays due to batching
of work, unnecessary steps, duplication of effort, and errors and rework).
Lean
Tip #1553 - Empower the People Operating the Process.
The
best person to improve a process is the person who carries out the process.
Utilize employee’s full skillsets—can someone be doing more? If the process is
improved, they will likely have time to take on higher level work.
Lean
Tip #1554 - Track Numbers and Manage by Evidence.
Sometimes
what should work well doesn’t. Test out your process, collect data on how well
it is working, highlight and eliminate errors, and seek continuous improvements
in value. Seek proof; don’t assume an improvement has been made.
Lean
Tip #1555 - Focus on Your Customers.
Ultimately,
what all customers want is value. Value creation occurs when the quality of
services received is perceived as high compared to their cost. What does your
customer want and how can you provide it better, faster, cheaper?
Lean
Tip #1556 - Don’t Try To Map All Your Processes at Once.
Some
businesses make the erroneous move of documenting all their processes at once.
This sort of exercise requires a significant amount of time and man-power
upfront with little or no value-add. Focus on mapping key business processes that
cut across the value chain where identifiable improvements can be made. Define
the scope, identify the business processes you need to focus on and concentrate
on those.
Lean Tip #1557 - The Process Mapping
Exercise Should Be Done Within A Well-Defined Framework.
Identify the standards, templates and
guidelines to be adopted for the exercise. The last thing you want is a process
repository with multiple notation types for the same type of event or activity.
It can easily become confusing for anyone reading the documents.
Business processes can be mapped to varying
levels of abstraction. The purpose of the mapping exercise will of course,
guide the process data you collect and the level of detail you go into. Agree
on what levels of abstraction the process documentation exercise should cover.
For example, will the mapping exercise cover all the processes within a
function (e.g. Planning) with the ability to drill down to sub-processes and
procedures?
Lean
Tip #1558 – Focus on Simplicity
There's
no benefit to building a repository that can only be understood by its
architect. Using complex notations or wording can quickly become overwhelming
for anyone reading the documents, thereby defeating the purpose of the
exercise. With process mapping efforts, this popular saying rings true: Less is
more.
Lean
Tip #1559 - Consider Training Team Members To Map
Not
all team members will be equally versed in conducting the process mapping
exercise. Set up a brief meeting/training session to bring everyone up to speed
on what is expected of them. This training should cover the standards to be
adopted, the tools to be used and any other unique requirements of the process
mapping exercise (e.g. it may be necessary to capture the accounting
transactions generated by each process step). Don’t assume everyone knows
exactly what to do.
Lean
Tip #1560 - Create Short-Term Goals to Keep Momentum High.
Documenting
processes can be a laborious exercise, from holding meetings with different
stakeholders, collecting process information, drawing process maps, creating
process documentation to obtaining signoffs. To keep morale and momentum high,
identify short-term wins and milestones to keep team members from lagging
behind or worse still, burning out.

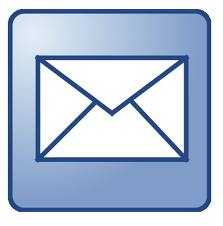




No comments:
Post a Comment