Unfortunately, safety measures and procedures can often turn
into more of a burden rather than an efficient system for safety for many
different organizations. Often the cost of the safety precautions and measures
taken is much higher than expected and can hinder the business as well as the
safety at the workplace.
The good news is - it is possible to reduce the cost for safety
measure without decreasing the quality and safety level. In fact, it can make
safety even more efficient.
The first thing you should do is measure the time which your personnel - from workers to supervisors and safety
professionals spend for safety related activities per day. If it turns out that
they are spending more than half of the work day or shift on safety specific
activities, you can do the math and see how much time is actually left for work
itself. If you are a production company and your employees all spend more than
50% of their time doing something other than actually producing things, neither
the owners, nor the management or your customers will be happy with the results.
The fact is, that most of the safety related activities and
procedures which you have implemented in your organization could be too time
consuming. For example, do you have complicated safety forms which need to be
completed? Or do your supervisors spend too much time investigating incidents
and monitoring the safety conditions? Do you have everyday safety training
which takes a lot of time?
These are some of the questions you need to ask yourself before
considering making improvements and simplifying your safety system, without
affecting its efficiency.
Here are some ideas how thinking lean can help you improve the
efficiency and effectivity of your safety system and procedures:
1.
Integrate the safety actions and procedures in your work and
support procedures. In other words, add
a safety process into the operational procedure itself. This way, the person
responsible for the job will be responsible for the specific safety procedure
for it. For example, add the lockout process for energy control in the work procedure.
This will make the entire workflow more efficient and actually safer.
2.
Integrate the procedures for safety analysis and job hazard risk
analysis into your work procedures as well.
3.
Integrate as much of the safety training into the work training
as possible, and also do specific
safety training for the people who are actually in risk of the specific
hazards, rather than wasting the time of all employees for all the various
risks. This will save time, and is actually a more efficient training method.
4.
Visualize the safe conditions. This means making unsafe or hazardous things
and processes more apparent for safety professionals or supervisors. Examples
include: defining the correct and safe body position, or position/condition of
potentially hazardous equipment, tools, and others. Use simple diagrams
including “right” and “wrong” conditions, allowing anybody passing by to see
that something is wrong.
5.
Watch out for employees who are taking shortcuts and are skipping important safety procedures or using the wrong
instruments in order to make their work easier or faster. Try to improve employee engagement, because such shortcuts can be dangerous and can lead to
serious injuries, damage and other problems. It is important that you inspect
the work process procedures, as well as any indications that shortcuts are
being taken, carefully conduct research and analysis for the reasons for this
nonconformity and take corrective actions. This can mean redesigning your work
procedure, so that the process becomes the shortcut. It is recommended that you
include the employees who used the shortcut to take part in the re-designing of
the work procedure. In many cases, this will lead to a more efficient and yet
safe operational procedure, and thus better productivity and improved safety in
your organization.
About the Author: Mike Pierce is an outdoorsman, lean
thinker, and footwear fanatic who manages the team at Mybootprint.com.
He also works on another site ShoeMatters.com that
helps people find high quality footwear for their needs.

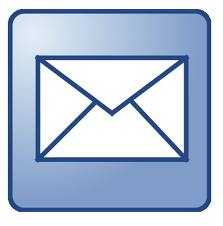





No comments:
Post a Comment