Click this link for A Lean Journey's Facebook Page Notes Feed.
Here is the next addition of tips from the Facebook page:
Lean
Tip #1681 - Encourage Employees to Recognize One Another
Of
course, a manager’s appreciation is important. But workplace recognition can
come from colleagues too. Consider creating “thank-you” slips for your staff
members to write notes of gratitude to coworkers. Expressing thanks, even for
small helpful acts, can go a long way toward building a cohesive team.
Lean
Tip #1682 - Maintain an Open-Door Policy
Happy
workplaces are environments where employees feel comfortable voicing their
ideas and concerns. Set the right tone by letting your employees know that you
welcome their thoughts for improving business operations and workplace culture.
Also, provide and ask for regular feedback. Don’t limit yourself to one format:
You could offer an idea board, suggestion box or monthly brown bag Q&A with
company leadership.
Lean
Tip #1683 - Recognize Outstanding Work
Want
to boost employee morale? Place an article in the company newsletter or a note
on a bulletin board in the office in recognition of a special achievement.
Praise employees for their good work in front of their peers. You don’t have to
spend a dime to reward hardworking employees for their actions and
achievements. Your gesture lets employees know their unique contributions and
positive attitudes make a difference for your company and the team.
Lean
Tip #1684 - Offer Professional Development Opportunities
Training
programs are an employee retention strategy that pays off big time. Your
employees benefit by expanding their skills. You benefit by getting a more
productive and versatile workforce. Everyone wins when you grow together.
Lean
Tip #1685 - Promote From Within
Your
employees will feel discouraged if they sense they’ll be sitting in their
current cubicle forever. If you want employees to invest in the business, then
invest in them, too. Many managers fail to consider that the talent they seek
could very well be right under their nose. Wise leaders consider “internal
employees” — professionals who are among your current workforce — first when a
position is created or vacated.
Lean
Tip #1686 - Keep Information Flowing
Employees
might worry when they don’t know what’s going on behind the scenes, creating an
environment in which speculation can take root and rumors thrive. If you don’t
give people information, they’re going to start making guesses. This doesn’t
mean employees have to know everything you know, but keeping the team informed
about issues that may affect them creates a sense of transparency. It lifts the
fog.
Lean
Tip #1687 - If You See Something You Like, Say It
This
doesn’t have to be constant, but if you see an employee going above and beyond,
thank them. Say how much you appreciate their work and how it’s not going
unnoticed. You may think this is unnecessary and it “goes without saying”
because they know what they’re doing is good, but trust us, a little positive
re-enforcement is always a good thing. Not to mention, this may cause some
friendly competition within the workplace -- which I have experienced firsthand
to help drive innovation and collaboration.
Lean
Tip #1688 - Give More Responsibility To Encourage Employee Empowerment
If
you want to empower your employees, hand them a little more responsibility. Let
them make important decisions in regard to the company. It’ll build your team
members' confidence when you recognize and trust their expertise.
Lean
Tip #1689 - Give Employees a Voice
Feeling
like they are part of the process, that their thoughts and ideas matter, and
that they have a voice in their work performance gives employees a sense that
they have an impact on their company. Plus, they’re on the front lines and know
best about how work should be performed. Actively soliciting employee feedback
and incorporating employee thoughts and ideas into how the organization
operates is a very effective way to engage employees.
Lean
Tip #1690 - Remember that Culture Happens from the Top Down
You
cannot delegate culture-building and then forget about it. Culture always
starts and ends with the leaders of an organization. If you have a toxic team
culture, you should look in the mirror. As the leader, always stay involved in
the staff culture. Be the biggest champion of your core values. Attend every
event. If you don’t set the tone for the culture you want or participate in all
the team events, how can you expect great culture from your staff?
Lean
Tip #1691 - Actively Manage Risks and Learn Early
Implementing
project risk management and early learning principles will help your team
identify roadblocks and issues before they occur and either eliminate them, or
manage them effectively. There has been a lot written on early learning
(iterative development, Agile, fast feedback, modular design). But no matter
what approach you choose, the purpose is the same - learn early and the impact
can be either entirely avoided or managed. Learn later, and it will cost the
project time and the organization money.
Lean
Tip #1692 - By Failing to Plan, You are Planning to Fail
Good
planning mitigates risks and promotes learning early. While planning, teams
consider, talk through, and eliminate ‘flow’ blockages before they occur. The
ROI on planning is huge. A good plan has enough detail for it to be predictive
of how much work is really going to be involved, and therefore when you will be
done. Records of past plans can also help, as an input into how much work will
really be involved in the various tasks, and how much unpredicted work there
typically is in a project.
Lean
Tip #1693 - Figure Out How the Work Gets Done.
We
have lots of assumptions about how work gets done that don’t mirror exactly
what happens. After all, during the day-to-day grind, we don’t think about how
we do the work, we often just do it. Ask an outside observer to record the
steps of the process in a way that he/she could repeat it themselves if they
had to, without assistance.
Lean
Tip #1694 - Remove Inefficiencies and Waste.
Once
you know what the workflow of your process looks like, take a second look at
any step in the process that doesn’t directly create value for the customer.
Manage, improve, and smooth your process flow to eliminate non-valued-added
activity (e.g., wasted time, wasted movement, wasted inventory due to
overproduction, customer delays, waiting for approvals, delays due to batching
of work, unnecessary steps, duplication of effort, and errors and rework).
Lean
Tip #1695 - Have a Strong Lean Improvement Strategy
You'll
need a solid plan and some attainable targets before implementing Lean. Utilize
checklists and to-do lists, and you’ll always be working towards a goal. Look
at every step in your process from the customer’s perspective: Is all that
you’re doing something that he or she would be willing to pay for? If not, it
is time to get back to the drawing board.

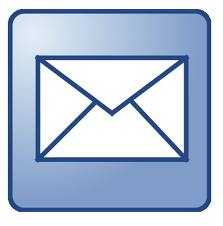




No comments:
Post a Comment