A common question I get on tours of our factory is how do you find time for improvement. My usual response is “we just do” but that is not entirely true.
“You will never find time for anything. If you want time you must make it.” – Charles Buxton (Philanthropist and Politician)
It is an age-old battle — production time versus improvement time. Two worthy rivals attempting to occupy the same narrow 24-hour space. The issue is not which is more important. Production is! This is as it should be: a company is in business to sell its products and services. It must first make them. And that takes time. Production time always comes first.
Too often improvement is left to chance and the ingenuity of the willing to eke out small pockets of time — and make magic happen. We all know these people. They see the vision burning brightly before them and are determined to make it happen. Time and again, these people prove — with their own mental, emotional, and physical health — the familiar adage: Where there’s a will, there’s a way.
Improvement doesn’t just happen. It takes time, and in the pressure pot of our day to day activities, there is never enough time to improve our situation. The structure of Lean permits and requires time be set aside for improvement. If managers do not definitively provide time for the task of improvement, then people will know that they are not serious about making improvement a formal part of the work.
One of the most common reasons I hear when improvement activity stops is ‘there is so much going on, we’re too busy to find time for improvement. The predominant culture in many organizations is on of firefighting – implementing temporary fixed to problems. Ultimately, however, fire-fighting organizations fail to solve problems adequately. Firefighting prevents us from getting to the root cause. And if we don’t get to the root of problem we will be right back to firefighting soon.
There are some ways to build continuous improvement into your business:
1. Remove roadblocks.
Management’s job is improvement. They must remove roadblocks that hinder this achievement. If managers do not take the time and make the effort to incorporate improvement in their work they are not serious about the effort. It takes time and effort to make changes in the way we do things, but it takes the time to consider and implement those changes if they are to survive in the long run.
2. Look for quick wins.
Don't start by trying to save a million dollars overnight. This is the type of work that makes people think they have no time for continuous improvement. After all, you can only work on so many of these projects at once before you really do run out of time - or you don’t even have the time to get started on any of them. Small, incremental changes can give you quick wins—without disrupting your operations or demanding a huge amount of effort.
3. Engage and develop entire team to solve problems.
Sometimes supervisors and managers think they need to implement all of the suggested improvements themselves, as in the old suggestion box model where employees point out problems and the boss fixes them (or ignores them or rejects their ideas). This approach results in the boss becoming a bottleneck.
In a successful culture of continuous improvement, managers accept that they can’t (or shouldn’t!) implement every little idea that their staff come up with. Instead, they empower the staff to act on their own ideas! Successful managers save time by developing their staff as critical thinkers and problem solvers.
4. Doing is more important than thinking
Improvement never comes to you while you are thinking about it. You are what you do. Knowledge is basically useless without action. Good things don't come to those that wait, they come to those that ask what they can do today to learn and move forward now.
5. Never stop.
It’s called “continuous” improvement for a reason. Once you’ve found your first quick win, start looking for the next one right away. A long-term commitment to continuous improvement will help you respond to growth and change—and keep your competitive edge sharp.
Adopting a culture of continuous improvement can benefit both you, your team and your business. Finding a suitable way to begin your never-ending quest toward it doesn’t need to keep you awake at night. Why don’t you start by implementing these 5 ways in order to set yourself up for all the benefits that come hand in hand with improving continuously!

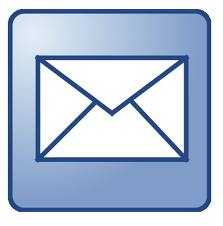





No comments:
Post a Comment