Leaders in
organizations across industries are always looking to “speed-up” a lean
transformation. Most organizations prefer to take small incremental steps away
from their current business model and target a set of initiatives that still
falls close to their existing position.
The challenge
with lean is that, despite its attraction to many executives who want to cut
costs and increase productivity, a lean process doesn’t happen overnight. There
are plenty of obstacles to overcome.
After 20 years
of leading manufacturing operations, implementing lean principles and
conducting hundreds of kaizens, there are some basic ways to accelerate your
Lean journey.
Develop
Culture
Lean is about
people. All successful and sustainable business change starts with top
management (leadership team). Culture
by design requires changing the way that people think and work. That’s
difficult to do, because people get comfortable with the way they are. You must
establish a foundation so that change can happen. The definition of ‘win’ has
to be shared and understood by everyone.
A new lean
culture will not develop unless the organization’s leadership team is willing
to model and be the examples of the new behaviors.
Leaders have
to Lead
Relentless
commitment from the leader or leadership is the basic requirement if you are
going to have a successful lean conversion. It’s the role of Lean leaders to
create an environment that fosters continuous improvement, by asking guiding
questions, supporting teams as they test hypotheses, and celebrating
improvements, in both performance and process.
Practicing Lean
management principles requires a shift in mindset: from that of a supervisor,
to that of a teacher and coach. Lean leaders must lead gently, by example,
ensuring that Lean principles are being applied with the right goal in mind: To
sustainably maximize the delivery of value to the customer.
Kaizen –
Develop Internal Capability
Kaizen events
are a powerful improvement tool because people are empowered to come up with
new ideas to help the business. Employees are isolated from their day-to-day
responsibilities and allowed to concentrate all their creativity and time on
problem-solving and improvement.
The purpose of
kaizen is to involve everyone, everywhere, everyday in making simple
improvements. These small improvements add up overtime and result in an
extraordinary and never-ending transformation of processes. Companies which use
Kaizens have found they generate energy among those who work in the area being
improved, and produce immediate gains in productivity and quality.
Kaizen also
improves people’s capability for thinking, judgment, and making fact-based
decisions. Kaizen teaches leaders how to develop other people so they can help
to quickly improve the business.
Bias for
Action
If you do
nothing, nothing changes. The
only cure for inactivity is action. That’s why the first step in creating a
successful culture of execution is creating a bias toward action. Get your teams out of the conference
room and into the gemba. From there, mandate a fast turnaround time, have them
quickly do a value stream map and root cause analysis for their actionable
items, and post their successes right away.
Teach Lean
to Everyone
The key to
implementing any new idea or concept is training. It must be top down training
so that everyone is on the same page. The more understanding of what lean
manufacturing is all about, why you are implementing it and the expected
benefits from it, the more likely you are to get buy-in.
It is very
important that everyone in the company become committed to lean culture. In
order to make the culture successful, managers and employees need to be aware
of waste within the company and be prepared to attack and eliminate it. Making
sure that the employees are empowered to do this, not just pushing the job off
on someone else, is imperative in the proper function of lean culture.
Ensuring
everyone is on the same page will help to avoid conflict. At the same time, it
is important to ensure people have the space in which to think about what
improvements they think need making.
Focus on Problems
and a Few Tools
One of the most
common mistakes that companies make when embarking on a Lean transformation is
trying to do too much at once. These “boil-the-ocean” initiatives are long,
costly and often end up stalling under the weight of their own ambition.
Lean
manufacturing consists of many different “tools”. There are a few tools that
can and should be used with any lean manufacturing initiative. Some of these
tools are 5-S (sort, set in order, shine, standardize and sustain), value
stream mapping, kanban, takt time, continuous flow, cellular manufacturing, TPM
(Total Productive Maintenance), SMED (single-minute exchange of die), OEE
(overall equipment effectiveness), line balancing, standardized operations,
seven wastes (muda), error-proofing, kaizen and root cause problem-solving.
The correct
approach to implementing lean manufacturing begins with an analysis of the
businesses needs, opportunities and challenges. Once these opportunities are
identified, the tools are used which will solve the issues.
It simply
wouldn’t be prudent to limit the success of a lean initiative to exclude any
tool if it was known to solve the problem at hand.
In other words,
the problems identify the tools rather than the tools being forced into the
organization.

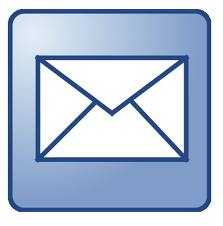





No comments:
Post a Comment