Here is the next addition of tips from the Facebook page:
Lean Tip #3511 – As a Leader Become a Project Sponsor
Are there processes within your department or business that you would love to see improved? Sponsor a Rapid Improvement Event in an area under your leadership. Partner with the event leader to develop the project charter. This will let your employees know that you are interested in their approach to making improvements in your part of the business and that you are sponsoring the improvement activity.
Lean Tip #3512 – Participate in a Kaizen Improvement Event
Most Kaizen improvement events are multiple days long. Clear your calendar and be an active participant without having decision making influence.
Realize that participants may be nervous by your attendance, so choose your involvement wisely. Hopefully, the improvement team is using a “no-rank” model of decision making where everyone in the event is equal.
Lean Tip #3513 – Attend Kaizen Event Readouts
When participants have spent several long days making improvements to a part of the business, nothing is more demoralizing than not having support when they conduct a readout. They are excited to share with leadership what they have accomplished. This goes a long way in sending the message you value your employees’ hard work and ideas.
Lean Tip #3514 – Thank Team Participants
While this may seem obvious, it is surprising how many times I have seen teams present information at the report out, and don’t get thanked for their efforts. Please, as leaders thank the team members for their efforts.
A simple thank you goes a long way with employees and helps increase employee engagement. They have worked hard to improve your business, thank them! Without them, your company will not grow or improve.
Lean Tip #3515 – Use Leader Standard Work
One of the best tools for sustaining Lean efforts is Leader Standard Work. While often associated with supervisor level employees, management should also follow it daily.
It provides an opportunity for you to become more consistent in your daily activities and shows that you are using the same methodologies as you are asking others to use. Your Leader Standard Work will differ from an operator or supervisor, but make sure you use and follow the same framework.
Lean Tip #3516 – Build on Your Company's Roots to Develop Your Own "Way"
Toyota has its way. You need to have your way. When Toyota works with companies to teach TPS, they insist that the companies develop their own system. Someone did something right to get you to this point. Build on that. Build on your company's heritage to identify what you stand for.
Lean will cut across functional/departmental boundaries that will eventually lead to a restructuring of responsibility for the major business processes rather than the current functional ownership of a department's activity.
Lean Tip #3517 – Hire or Develop Lean Leaders and Develop a Succession System
The key is not to take ownership of the plan but to provide conditions in which the team can implement Lean. The aim of this approach is to create a nucleus of people who are trained in the Lean tools and techniques, who have experienced Lean through hands-on application and who can then with some external support move on to help others create lean processes by transferring their knowledge.
Lean Tip #3518 – Start with Value Stream Pilots to Demonstrate Lean as a System and Provide a "Go See" Model
One of the key lean tools is that of "Value Stream Mapping". This tool when used correctly enables us to create a map of both value and waste in a given process. This map can then be used to understand the waste and its causes before moving on to remove it so that value flows without interruption of waste.
When developing the current state map, future state map, and action plan for implementation, use a cross-functional group consisting of managers who can authorize resources and doers who are part of the process being mapped. Value stream mapping should be applied only to specific product families that will be immediately transformed.
Lean Tip #3519 – Use Kaizen Workshops to Teach and Make Rapid Changes
Use a talented and experienced facilitator who has a deep understanding of lean tools and philosophy but keep training focused on a specific problem. This helps to keep the training relevant to real-world situations and ensures that there are tangible outcomes from training activity. The kaizen might have an objective to reduce setup time from 80 minutes to 60 minutes in four days, for instance.
Lean Tip #3520 – Ensure that All Members of Staff are Correctly Coached
This avoids conflict and delivers a management group that can facilitate change with the teams working for them and so remove waste efficiently. In practice, this means learn by doing first and training second.
Unfortunately, you cannot PowerPoint your way to Lean. The Toyota Way – often held up as the epitome of Lean - is about learning by doing. In the early stages of lean transformation there should be at least 80% doing and 20% training and informing.
The Toyota approach to training, for instance, is to put people in difficult situations and let them solve their way out of the problems.
Lean Tip #3521 – Review Your Processes and Analyze
Take a look at your processes and see what immediate changes can be made. For example, are you experiencing overproduction or excess delays? Perhaps you're shipping items in too many batches when they could be combined together for greater efficiency and cost-saving? Are there problems being caused by the office not processing information quickly or correctly, or perhaps items are coming out with defects?
It is important to look out for where your most obvious problems are and start with these as your initial changes. Ultimately, any customer just wants the best value and service available to them. With all your processes, it is important to ask if this is what you're offering in relation to the cost. Think about what the customer wants and whether you can improve on this to give them results quicker, more cost-effective and to a higher quality.
Lean Tip #3522 – Develop a Culture of Quality Over Quantity
If you're experiencing problems with your output, it may be that your staff are trying to work too fast to meet unattainable goals and are subsequently not maintaining quality standards leading to higher levels of defects or customer dissatisfaction.
Getting it right the first-time round is best for efficiency, so ensure staff realize that quality takes precedence. Don't overburden staff and allow them the time to stop and fix problems in order to always do things correctly.
Accuracy, productivity, and motivation can also be encouraged by introducing employee incentives in the workplace like rewards for the employee of the month or monthly team treats for good performance.
Lean Tip #3523 – Standardize Your Tasks When Possible
Not all tasks can be standardized but putting clear processes in place when possible will ensure tasks are completed to a standard system; making it efficient, productive and lowering the risk of errors. It also means when staff leave, they don't necessarily take their knowledge and processes with them – and when new staff arrive, they can be quickly and easily trained. This also ensures you can spot when something is not working or not being done properly.
Lean Tip #3524 – Make Decisions Slowly, and Implement Them Quickly
When it comes to deciding what will bring about lean management in your workplace, it's important to spend time ensuring it is the right decision and getting a strong consensus from the whole team. Nothing wastes time more than making one decision and changing it the next week. However, once you have decided on the right answer, you need to bring about the implementation of it as quickly as you can.
Lean Tip #3525 – Think Outside the Box
Sometimes the processes that will save you the most time and money won't be the most conventional. They won't fit within the boundaries of common sense and standard rules, so it is important to always think outside of these parameters. Is there something else you haven't considered? Be constantly aware that the answer may not be right in front of you.

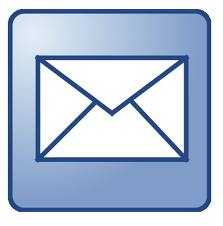




