Click this link for A Lean Journey's Facebook Page Notes Feed.
Here is the next addition of tips from the Facebook page:
Lean
Tip #796 - Everything is Important But Some Things are More Important than the
Others
A
cornerstone of Lean Six Sigma is the Pareto-law or 80/20 law. Choosing the
right project, focusing the project on the key problems, selecting the main
causes of the problem or defining the improvement actions is important.
Determine which activities/problems are most important using data, not
perceptions.
Lean
Tip #797 - Don’t Take on Massive Projects
Massive
projects, taking place over long stretches of time, can encourage
procrastination – as far-off goals are less motivating – and can be
discouraging since your team will feel that they are achieving less. Instead,
try to work on smaller and more focused projects, which will be far easier for
your team to concentrate on.
Lean
Tip #798 - Middle Management is Essential For Motivating Your Team
In
order to properly motivate and keep a close eye on your team, Middle Management
is essential. Make sure that your project leaders are keeping them in the loop,
and they will ensure a smooth and connected working environment.
Lean
Tip #799 - Make Sure Your Leaders are Active Teachers
All
leaders, and especially senior leaders, have to remain fully engaged. It is
their responsibility to ensure that the team successfully improves, through
leading process improvement activities. The project and the team will not be successful
if leaders delegate their responsibilities to others – this will lead to a lack
of strong leadership and possibly failed improvement activities.
Lean
Tip #800 - Everyone Can Solve Problems
Avoid
thinking that experts are always needed. Although experts can be essential, on
a day to day basis, everyone can use basic six sigma tools and think creatively
and practically. Don’t let your team get stuck too often waiting for an
expert’s opinion.
Lean
Tip #801 - Create Organizing Systems.
Being
organized saves tons of time, and you don’t have to be the most ultra-organized
person in the world either. Systems aren’t complicated to implement.
Create
a filing system for documents. Make sure all items have a place to be stored in
your dwelling. Streamline, streamline, streamline.
Lean
Tip #802 - Constantly Improve Your Process
Change
is good, especially when it translates to getting things done with more
efficiency, more expediency, or less cost. Be on the lookout for ways to do
things better – it could mean you have an easier time managing your workday.
Lean
Tip #803 - Think of how to do it, not why it cannot be done.
The
pessimist will create all kinds of reasons that something can't be done. The optimistic,
forward thinker, on the other hand, knows that "if the why is strong
enough, the how will come."
Focus
on the outcome. Then, come up with all the ways that the outcome could possibly
be accomplished.
Lean
Tip #804 - Do not seek perfection. Do it right away even if for only 50% of the
target.
If
we all waited for perfection, we'd still be reading by candlelight and riding
horses to work. Once you get to a certain point (whether it's 50% or 80%, or
another number that makes sense), then run with it. In other words, take
action. Then, adjust as you go along.
Lean
Tip #805 - Kaizen ideas are infinite.
Kaizen
is a process of learning and growing, steadily and continually. There are
always ways to "tweak" elements of your life in order to improve
them. It has been said that life is a journey, not a destination. And practicing the philosophy of continuous improvement,
of kaizen, will help you to make the most of that journey!
Lean
Tip #806 - Question Everything. Ask "Why" Five Times.
A
brilliantly simple root cause problem-solving tool, asking why five times
becomes easier the more you do it. Adopting this as a default way of looking at
things will aid, not only your problem solving, but other areas, too.
Lean
Tip #807 - Ideas are Infinite. Execution is the Key.
This
simple maxim is often overlooked as people get caught up in meetings and so on.
You've got to be the change you want to see, not the change you'd like to see.
It's the same as not confusing better with best. You want to move to better
right away, not take forever working out what "best" looks like.
Lean
Tip #808 - Kaizen Starts With Taking a Look at the Actual Place of Work.
Continuous
improvement efforts must start with a trip to the gemba. The gemba might often
be the factory floor, but people forget about Lean in the office, where half of
the work starts out being late! It's easy to see waste on the floor, but it's
harder (at first) to see waste in the office or other value streams. Going to
the gemba will make it easier.
Lean
Tip #809 - Kaizen Requires a Bias for Action.
Get
your teams out of the conference room and into the gemba. From there, mandate a
fast turnaround time, have them quickly do a value stream map and root cause
analysis for their actionable items, and post their successes right away.
Lean
Tip #810 - Discard Conventional Fixed Ideas.
Part
of problem solving is thinking outside of the box. Encourage people to think
this way and not in the same old way that got them into the problem to begin
with! Think about how to do it, not why it can't be done. I often hear,
"We tried that before and it didn't work." They may have had a good
idea, but the chances are that they didn't include the accountability portion.
Without accountability, you will not have sustainability.

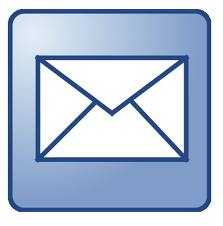





No comments:
Post a Comment