Problems are expected in the course of business. A successful organization is not determined by the absence of problems. Rather, success is measured by how we solve the problems that do emerge.
The seven-step “root cause” problem solving process is a logical, commonsense method to solve any type of problem. It provides a road map to help everyone solve problems during the improvement journey. It suggests what materials and information are needed to resolve an emergent issue. And it provides a record of the decision making process. If the solution we select does not bring the desired results, we can review our steps and assumptions and make subsequent adjustments.
Versions of the problem solving process exist under a variety of acronyms. Regardless of the specific model employed, there are seven universal steps:
- Select the issue.
- Search for data to describe the situation.
- Analyze the facts to obtain root cause(s) of the performance gap.
- Select a solution.
- Conduct a pilot test.
- Evaluate performance.
- Standardize the gains, reflect, and repeat the process.
1. Select the Issue. Start with the voice of the customer. Even if your work group does not have direct contact with the external customer, take the time to identify how your activity affects the customer. Then create a measurable problem statement, such as “reduce late deliveries.” Specify the measurable performance gap you wish to close.
2. Search for the data to describe the current situation. Gather all the relevant facts. In the early stages of any problem solving process, data are often scarce, and it’s tempting to accelerate the process by moving right into action. But take the time to search for the date to describe the current situation. Use the seven basic quality tools (fishbone diagram, Pareto chart, histogram, line chart, scatter diagram, control chart, and check sheets) to analyze the data and visually display the facts of the story. New ways of thinking will emerge when the data have a chance to speak.
3. Analyze the facts to obtain the root cause(s). Problems are often complex. Often, what we view as the problem is merely the symptom of a deeper, more complex problem with multiple contributing factors. In other words, the problem manifests in one area, but the “root cause(s)” of the problem lies elsewhere. One simple method to identify the root cause of a problem is called the “5 whys.” Simply ask “why?” five times. By the time you get to the fifth “why,’ you are usually down to bedrock. Another technique used to identify root causes is the fishbone diagram (also called the Ishikawa diagram, or the cause and effect diagram). The main purpose of the technique is to identify and map the major contributing factors to the development of a problem.
4. Select a solution. Unlike many mathematical problems, which allow for only one answer, quality problems have many possible solutions. So don’t jump to the conclusion that on particular solution is the only solution. Take the time to identify and consider as many ideas as possible. This is perhaps the most creative step in the problem solving process. Do not judge the quality of your solutions, even the crazy ones, until you exhaust the brainstorming process. Then, select an approach, preferably one that focuses on process improvement and that is financially feasible, has the best chance of being implemented and will have a high impact on the problem.
5. Conduct a pilot test. Take the time to do a test run on the solution. Make individual responsibilities clear and establish a daily schedule for the improvement plan. Notify anybody who might be affected by your changes before you begin implementation.
6. Evaluate performance. How well have you done? Is the problem subsiding? Do you see any improvement? Are there any assumptions that need to be modified? Check whether your solution produced the desired affect. If the results are not satisfactory, revisit the earlier steps in the problem solving process.
7. Standardize the gains, reflect, and repeat. Once you see that the solution is working, take action to maintain the gain. Standardize the solution so that you can prevent the very improvements you worked so hard to accomplish from being neglected or replaced over time with past practices. Gather data until the benefits stabilize. After you confirm that you achieved your desired effect, communicate the improvement.
The seven step problem solving process is a powerful mechanism to solve problems once and for all. In the end, an improvement is never an improvement until every step, including follow up, is implemented, then look for new ways to improve. Continuous improvement is just that – continuous.

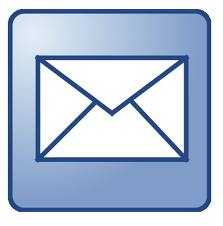





No comments:
Post a Comment