Lean
Manufacturing is a business improvement philosophy that has developed over many
years (as well as a collection of lean manufacturing tools), it is a method to
better focus your business on the true needs of the customer to help you
prevent waste from being built into your system. When properly implemented,
lean manufacturing provides many advantages, which include improving flow
(material, people, information, and work) and eliminating waste.
I detail many
of these benefits below:
Improved Quality – A lot of the activity in a lean
environment is geared towards improving quality. As quality issues arise,
problem solving techniques are used to root cause the problem. From there,
mistake proofing is put in place to strengthen the process and prevent recurrence.
As a result, the quality of your product will be improved.
Increased Productivity and Flexibility - In a lean business, employees move
parts through the manufacturing process a single piece at a time instead of in
batches. The single-piece flow increases productivity and improves the
flexibility in production processes. Companies using lean manufacturing
processes reduce the amount of time required to manufacture a product, which
increases the ability to respond to customer orders.
Total Company Involvement – Lean is meant to involve the whole
company. It is not intended to be put into action in only one area. It is a
management philosophy which should include every part of your organization.
This helps promote the concept that everyone in the company is part of the
team.
Better Use of Employees – Lean cuts overproduction by adjusting
production to meet customer demand, and it simplifies the product to eliminate
extra processing. These activities help your company meet customer demand with
fewer employees. Fortunately, this doesn’t require layoffs. As employees are
given a chance to increase their skills and abilities, and to fully develop
their talent, they will be more productive and effective.
Increased Efficiency – Line balancing will ensure each person
in the process is working in the most efficient manner. Standardized work will
ensure they are doing it correctly following the same method every time. This
leads to repeatability and increased efficiencies.
Optimized Space – Lean principles help reduce excess
inventory and eliminate overproducing products. When you are producing no more
than what the customer requires and you are shipping all of your products
quickly, there will be more physical space on the production floor. This
environment is easier to organize and safer to work in.
Safer Work Environment – Visual management and 5S will help
identify when things are out of place. When unnecessary elements are removed
from the operation, the workplace becomes much more organized. And an organized
work environment is a safe work environment.
Improved Employee Morale – Lean manufacturing methods, when
implemented successfully, empower employees to participate in improvements,
which can improve worker morale Employee involvement and empowerment will make
all members of your company feel like a contributing part of the team. And the
reduction of uncertainty in the workplace, as a result of lean, will reduce
stress in your team members and lead to improved employee morale.
Lean principles
can provide substantial gains for organizations and their employees. By
implementing Lean you will become a far more competitive and effective business
enabling you to grow your business further.

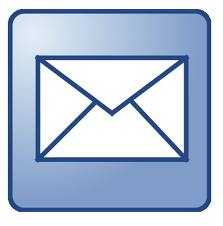





No comments:
Post a Comment