We’ve all heard
the saying, it takes a village. In a Lean organization this is absolutely
true. We all have roles in our
organizations but it takes teamwork to be successful. Lean takes everyone
working together.
Change must
happen not to, but with employees. Management has to invest in the employees’
understanding of this new environment, create opportunities for employees to
develop and run with ideas, and develop a trusting relationship.
Whether an
employee is a material handler, a machine operator, an assembler, or an
inspector, the plant experience changes as a result of the lean transformation.
The following
abilities are essential for a worker to possess in Lean manufacturing
environment:
Willingness to learn new skills. The ability to perform a variety of
tasks is key to flexibility, which is critical in the Lean enterprise. Being
willing to participate in cross training efforts, where workers learn and teach
new skills, is the first step. In addition, accepting different types of
responsibilities, which may have previously belonged to supervisors, may be
required. Tasks such as machine and equipment troubleshooting and problem
solving, data collection and analysis, and production scheduling are typical of
the tasks workers may face. As workers learn more skills and accept more
responsibilities, they will be less reliant on others and more valuable to the
organization.
Offer ideas for improvement. We all recognize that management does
not have all the answers and must frequently rely on the workers to find ways
to make things better. Instead of just “the usual few” workers offering ideas,
this type of effort is required of everyone. Whether it is an idea for
eliminating waste in an operation, simplifying scheduling, combining operations
to improve throughput time or an entirely different approach to making a part,
every worker must recognize the importance of contributing something.
Share responsibility for implementing
change. Management can
no longer be the sole driver of change, and therefore, workers cannot sit back
and take a wait-and-see approach. Once a consensus is achieved to change
something, everyone must buy in and strive for success. Passive behavior and
the “blame game” must be discouraged. Giving less than the best effort to
ensure a successful transition is a missed opportunity that may not present
itself again.
Transformation
to a Lean workplace requires extensive collaboration from everyone for it to
take hold. Adopting these abilities will lead to a successful Lean transition.
It takes a village to transform an organization.

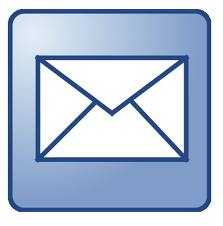





No comments:
Post a Comment