At the beginning of this year I attended a Connecticut Business and Industry Association (CBIA) Workshop on Boost Productivity with Smarter Workplace Safety. The workshop was conducted by CONNSTEP that is a Manufacturing Extension Program (MEP) partner that I have worked with many times over the past twenty years. The training session was led by Matin Karbassioon, CONNSTEP Lean Consultant, and Nick Wallick, Lean Analyst for CT Training and Consulting Institute.
The approach proposed during this
workshop is to utilize lean principles and practices currently in use in many
manufacturing companies and then incorporate health and
safety and sustainability aspects into these standard lean tools. An example is the Value Stream Mapping tool
which is used to define both information and material flow, to identify value-add
and non-value-add steps (waste), and opportunities for improvement. The workshop proposed addition of safety and
environmental considerations as part of this process which could be an
effective approach if implemented properly and supported by leadership. An example of a standard product
manufacturing view is shown in Figure 1.
Figure 1 Standard
VSM Map
The VSM is used to identify
opportunities to move from a current state to some improved future state. The workshop proposes to add safety
improvements to this analysis as illustrated below in Figure 2.
Figure 2- VSM with
Safety Opportunities
Following
this progression in thinking, we can also use the lean tools to analyze current natural resource
usages and identify opportunities for improvement. Figures 3 - 5 illustrate how this approach
could be incorporated into the “standard” lean process.
Figure 3 - VSM with
EHS Info Added
Figure 4 - VSM with
Material Usage Example
Figure 5- VSM
Overview with EHS Info
The
process mapping approach was discussed in more detail and additional
information can be obtained by review of the workshop presentation that is
provided as a separate document.
Discussion
of this approach included identifying links to safety related to the “8 wastes”
of the lean process: Defects, Overproductions, Waiting, Non-utilized people,
Transportation, Inventory, Motion, and Excess Processing. I’ve summarized some of these relationships in
the table below to illustrate the idea.
Waste Type
|
Links to
Safety
|
Defects
|
1. Defect prevention requires
less work and involves fewer injury exposures than defect discovery and repair
2. High levels of defects may
also signal poor housekeeping and/or lighting which may create other safety
issues such as distraction and eye strain
|
Overproduction
|
1. Overproduction indicates
that workers may be working faster than needed by the next process, which can
increase the risk of a repetitive strain injury.
2. Making more than is needed
may also result in clutter and poor housekeeping and increased number of
accidents. (balanced workload based on customer demand rate reduces these
risks and decreases the likelihood of increased work in process inventory)
|
Waiting
|
1.
Delays
and time wasted due to poor material and information flow can impact employee
motivation and increase the risk of falls and overexertion as workers rush to
catch up.
|
Non-utilized
People
|
1.
Risk
of complacency and loss of focus when performing monotonous tasks.
|
Transportation
|
1.
Excessive
product movement increases exposure to material handling and industrial truck
injuries.
|
Excess
Inventory
|
1. Excess work in process
between operations (due to large lot production or processes with long cycle
times) impedes movement, increases the risk of trip hazards, distractions,
blind spots for pedestrians and fork lifts, as well as manual handling
injuries.
2. Excess raw material
inventory will result in temporary (often unsafe) storage locations creating
obstacles to safe movement of employees
|
Motion
|
1.
Unnecessary
motions such as reaching over the head for a tool or searching for one,
instead of having it within normal reaching distance, at the point of use,
are both wasteful and hazardous.
|
Excess
Processing
|
1. Inefficient work flow and
extra processing steps such as avoidable reaching, twisting and material
handling tasks increase overexertion risks.
2. Process steps that
absolutely add no value to the product of service being provided may help
increase EHS risks
|
Finally,
the 5S process was discussed as one of the best means of creating and
maintaining conditions favorable to a safe and healthy workplace. This process has five steps or levels
although there is a school of thought that suggests adding a 6th S
for “Safety” but careful adherence to the 5S process will result in safety
improvements. The 5S steps are:
Sort
– identify and remove clutter
Set
(in order) – identify locations for frequently used items and ensure they are
kept in their place
Shine
– clean and inspect everything inside and out (inspection provides
opportunities for improvement)
Standardize
– Create rules to maintain the first 3s’s
Sustain
– Adherence to the rules and proper training of all workers
National studies show a strong correlation between high incident rates and lean implementations where strong safety programs were not present.
How do you incorporate safety into your lean efforts?

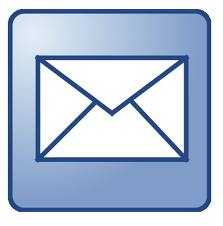





No comments:
Post a Comment