It’s a common occurrence in business: a manager is gearing up for a major project or is ready to propose a change in policy. They’ve spent months working on the proposal, conducting research, and gathering information to make it successful. But when the proposal is presented in a meeting there is a clash of opinions, changes are rejected, and progress is seriously hindered. In order for policy changes or projects to succeed, a consensus among team members must be met, and this can be done with nemawashi.
A
literal translation of nemawashi is “going around the roots,” referring to the
transplant process of a plant or tree. Extra
effort is taken by introducing to dirt from the new location to the tree and digging
around the roots to move the tree. Transplanting a tree takes time and
preparation to ensure survival in the new environment. Nemawashi is an
important part of not only the Toyota Production System but it is
also deeply embedded into the culture of Japan.
The
same concept can be translated as transplanting ideas to minds for nurturing a
successful proposal. In business, nemawashi is the first step in the decision-making
process and works to develop a foundation of consensus before implementing
changes to a process or project. Through small and informal meetings, managers
gather feedback, suggestions, and opinions and can use this to present a
successful proposal. The free exchange of ideas promotes continuous
improvement and like other Lean tools, relies on involvement from
workers on all levels. When a manager presents his proposal to others in a
meeting after using the nemawashi mindset, everyone is on the same page and has
a better understanding of the proposal, and by this time changes have been
already made based on employee feedback. The project can be carried out
smoothly and successfully.
How to Apply the
Nemawashi Philosophy
Nemawashi
is more ambiguous than some of the other Lean tools; there is no exact
framework to follow or steps that must be completed. Each nemawashi process
will be different than the last, and over time you will see how you can
effectively practice nemawashi in your own facility.
However
you decide to go about it, the process typically begins with managers and
supervisors sharing information. For instance, if you are going to propose a
change to part of the manufacturing process, you would send out information
about the condition of the process, why the current process is wasteful,
possible countermeasures, and any other relevant information to all employees
involved in the process.
After
employees get a chance to review the info, the manager will begin to meet with
them for a conversation. This can either be done one-on-one or in small groups,
but it is important to give the workers an opportunity to share their opinion.
Leaders will need to take the time to listen and show that their suggestions
are taken under consideration. From there, the proposal can be refined or even
tossed depending on the consensus, a new document with the revised project
proposal is create, and a formal meeting is scheduled to present the proposal.
By this time, support has already been gathered and any kinks in the plan have
been smoothed out. Employees have an understanding of the proposal and will be
able to effectively help implement any changes.
Leaders
and managers who take the extra time and effort to listen and learn to
employees, the nemawashi mindset truly allows changes to be carried out with
all parties consenting of decisions. The success of a project usually relies on
support from everyone involved, and nemawashi builds that consensus behind the
scenes, before any changes are even made.
About the
Author:
Jesse Allred is a blog writer for Creative Safety Supply leaders
in visual safety and Lean manufacturing resources. She enjoys sharing
information and advice for facilities to achieve efficiency while keeping
employees safe.

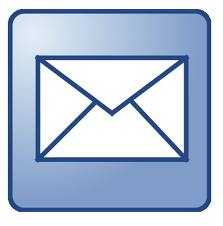





No comments:
Post a Comment