Here is the next addition of tips from the Facebook page:
Lean Tip #2896 – Focus on Small Changes
Approach change in small, incremental steps; if you improve by just 1% every day for a year, you’ll be 37 times better than when you started. Test and implement small changes. This increases the speed of improvement and reduces the pressures and risks of implementing a major change.
To this end, focus your improvements on solving the root causes of issues. This allows employees to catch and contain small issues before they become larger and costlier to eliminate, and it prevents the same problems from reoccurring.
Lean Tip #2897 – Document Your Process and Performance Before and After Improvements Have Been Implemented
In kaizen, it’s important to “speak with data and manage with facts.” In order to evaluate improvements objectively, existing procedures must be standardized and documented. Mapping the process’s initial state can help you identify wastes and areas for improvement and provide a benchmark for improvement.
Measuring performance against existing benchmarks allows you to demonstrate ROI from your kaizen efforts and keep the company aligned around improvement. It also allows you to identify areas where your efforts are working–or not–so you can make strategic decisions about future improvements.
In order to measure performance objectively, you should identify metrics that quantify improvements. These may include metrics revolving around quality, cost, resource utilization, customer satisfaction, space utilization, staff efficiency, and other KPIs.
Lean Tip #2898 – Standardizing Work is Crucial to Kaizen
In order for improvements to last, they must be standardized and repeatable. Standardizing work is crucial to kaizen because it creates a baseline for improvement. When you make improvements to a process, it’s essential to document the new standard work in order to sustain the improvements and create a new baseline. Standard work also reduces variability in processes and promotes discipline, which is essential for continuous improvement efforts to take root.
Lean Tip #2899 – Create Your Own Kaizen Guidelines
While there are many resources available to guide you through your kaizen efforts, it’s important to personally understand your company’s kaizen journey. Reflecting on your kaizen efforts after improvements have been implemented is an important part of the continuous improvement cycle.
As you reflect on your efforts, develop your own kaizen guidelines. Start by creating guidelines based on your own experiences improving the workplace. Keep in mind that these guidelines should be for your colleagues, your successors, and yourself to understand the problems you have overcome. These guidelines will ultimately help you as you approach your next challenge.
Lean Tip #2900 – Enforce Improvements
It’s easy for employees to regress to their old ways. Enforcing the changes you’ve made to your processes is important for the improvements you’ve made to last, and it’s key to sustaining continuous improvement in the long term.
Documenting improvements, making sure standard work is up-to-date, and training employees on new procedures can help sustain the progress you’ve made in your continuous improvement efforts.
Lean Tip #2901 – Problem Solving Starts With Clearly Defining The Problem.
It’s hard to solve a nebulous problem you never took the time to clearly define. No workplace is perfect, and there are usually a variety of interrelated problems that can be solved at any one time. If you find yourself getting overwhelmed and distracted during the problem-solving process, go back to step one and make sure you are approaching a singular problem.
Lean Tip #2902 – Focus on the Solutions, Not the Problems.
It’s easy to become hyper focused on the conditions that created the problem. Shifting your focus away from the current problem to possible outcomes and solutions can give you a more positive outlook and open your eyes to new solutions.
Lean Tip #2903 – List Out as Many Solutions as Possible
Try to come up with ‘ALL POSSIBLE SOLUTIONS’ – even if they seem ridiculous at first. It’s important you keep an open mind to boost creative thinking, which can trigger potential solutions.
Coming from many years in industry, it is drummed into you that ‘No idea is a bad idea’ and this aids creative thinking in brainstorms and other problem-solving techniques.
Whatever you do, do not ridicule yourself for coming up with ‘stupid solutions’ as it’s often the crazy ideas that trigger other more viable solutions.
Lean Tip #2904 – Visualize the Problem
Try and document a picture of the process depending on the problem. This may or may not be relevant, but we all know pictorial representations often help. Draw a simple diagram without worrying about technical conventions, specific constraints etc. A simple picture diagram can help visualize the most complex of problems in any area. Use any simple tool like PowerPoint, white boards, sheets, and papers and never shy away from starting to draw these on the fly if understanding a problem is becoming a challenge.
Lean Tip #2905 – Learn from the Past
When you’re approaching a problem, consider any similarities it might have with a problem you managed to solve in a previous role. What did you do to solve this problem? Did it work? How could you improve on it? Learn from your successes and mistakes.
Lean Tip #2906 – Be Simple but Creative in your Solution
Building a simple solution does not mean trivializing the problem which you are looking to solve. The majority of the time, complex solutions are devised for a problem if the above points i.e. understanding the right problem, understanding the fundamentals of the problem, articulating the problem and focusing on the root cause, are not considered.
Give your brain a break, try to baseline your thoughts and stop when you have understood the problem and fundamentals behind it. It is always best to de-clutter your brain and then subsequently attack and approach the problem efficiently. Take a break, then recap and work on a simple solution to the right problem you are looking to solve.
Be creative in your problem solving. This has got nothing to do with how much creative ability you have, it’s basically about thinking of solutions from a different perspective rather than a perspective with which the problem you are looking to solve was built or on how the problem came into existence. This is quite an important message and is highlighted in one of my favorite quotes from Einstein.
Lean Tip #2907 – Don’t Settle for the First, Most Obvious Solutions
Because problem-solving strategies often need to be found and implemented quickly, it can be tempting to use the first solution that comes to mind. But is it the most innovative? And does it have the ability to solve the problem permanently? You don’t have to ignore or reject the first strategy that comes to mind, but be willing to park it until you’ve completed your problem-solving steps and have considered the alternatives.
Lean Tip #2908 – Engage the Best People
When you’ve found the best problem-solving strategy for the task at hand, know how to engage the best people and resources to resolve the problem. The best skills may come from an internal department, from external contractors or freelancers or from a combination of both. Knowing how and when to engage the best people is a key problem-solving skill.
Lean Tip #2909 – Be Efficient at Testing and Learning
Be prepared to test the best problem-solving strategies efficiently and learn from what is applied. Document the process from beginning to end to understand what works, what doesn’t, and the point at which solutions failed to solve the problem. Having comprehensive documentation will be beneficial when you do find the right solution, and will serve as a valuable guide for colleagues and teams who may later face the same challenges.
Lean Tip #2910 – Identify Problems Before They Occur
Someone with brilliant problem-solving skills
(and very likely the respected leaders you admire) will have, over time,
developed the ability to identify problems before they occur. While this
doesn’t mean they can always be avoided, it does allow more time to establish
and implement the best problem-solving strategy. This special skill also relies
on extraordinary knowledge of an organization, its values and processes, the
industry it exists within and broader market trends.

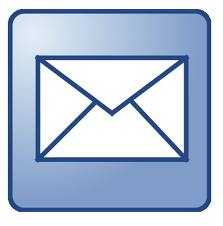




No comments:
Post a Comment