Lean manufacturing practices and sustainability are conceptually similar in that both seek to maximize organizational efficiency. Where they differ is in where the boundaries are drawn, and in how waste is defined. Sustainability expands the definition of waste to include the wider range of consequences of business actions including environmental and social consequences. Lean processes are inherently less wasteful and in this sense promoting lean processes can help organizations become more sustainable.
Many manufacturers know the benefits of lean manufacturing: higher productivity, better quality, reduced cycle time, plus enhanced employee engagement. Lean is excellent at marshaling different groups and individuals into a high performing team focused on rooting out waste.
A Lean organization is commonly characterized by the elimination of the following seven wastes (Ohno’s wastes):
- Waste of overproduction (waste from faster than necessary pace);
- Waste of waiting;
- Waste of transport (conveyance);
- Waste from inappropriate processing;
- Waste due to unnecessary inventory (excess inventory);
- Waste due to unnecessary motion; and
- Waste due to defects.
By adopting Lean Principles, businesses can eliminate or reduce wasteful processes that can slow down the manufacturing procedure and add to costs.
In recent years many companies have established a fundamental goal to minimize the environmental impact while maintaining high quality and service for all business processes and products. This is commonly referred to as sustainability or green manufacturing. According to the Department of Commerce, “Sustainable manufacturing is the creation of manufactured products that use processes that minimize negative environmental impacts, conserve energy and natural resources, are safe for employees, communities, and consumers and are economically sound.”
When implementing lean within our organizations, equipment reliability is a predominant foundational element that enables lean operational performance. Embracing green manufacturing requires giving more focus to environmental and energy concerns during the implementation of reliability improvement projects. Improvements geared toward improving equipment reliability have distinct linkages to environmental performance.
As most manufacturers are starting to realize, the quest to become green takes them right back to Lean. Applying ‘Lean Principles’ – a systematic approach to identifying and eliminating waste through continuous improvement - is one of the key ways to enhance environmental performance. By applying the tools, systems thinking, and lessons learned from the process improvement methodology they can effectively operationalize sustainability.
Lean and sustainability are conceptually similar. Both seek to maximize the efficiency of a system. This is accomplished through waste and time minimization. The difference lies in where this system (or process) boundary is drawn and how, and in how waste is defined. Lean sees waste as non-value added to the customer; green sees waste as extraction and consequential disposal of resources at rates or in forms beyond that which nature can absorb.
When companies expand the definition of waste to include not only product and process waste, but also the business consequences of unsustainable practices, Ohno’s list of wastes takes a different form:
- Waste of natural resources
- Waste of human potential
- Waste due to emissions
- Waste from byproducts (reuse potential)
- Terminal waste, waste from by-products that have not further usefulness
- Energy waste
- Waste of the unneeded (e.g., packaging)
There are also multiple Lean benefits from a green perspective including limitation of over-production. Other benefits include the reduction of obsolete equipment and the ability to provide efficient systems, thereby reducing both energy and materials usage.
Lean manufacturing practices, which are at the very core of sustainability, save time and money — an absolutely necessity in today’s competitive global marketplace. While the pursuit of Green and Lean is not a destination but a journey it is clear that organizations that stretch themselves to build a culture around the values of Sustainability, Excellence, and Equity will ultimately have a big advantage those who do not. Isn’t the ultimate definition of “sustainable manufacturing” to be able to compete and not only survive, but thrive?

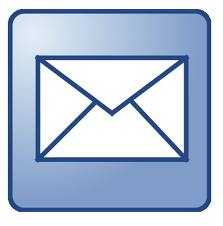




