"Without reflection, we go blindly on our way, creating more unintended consequences, and failing to achieve anything useful." — Margaret J. Wheatley
Great
leaders pause and reflect on a regular basis; leaders at their best renew
themselves daily. Without time for reflection, a leader is likely to miss
important cues, to forget to do the more important things. They don’t see
opportunities because they are hidden by the busy and trivial things. Over
time, the leader without time for reflection is doomed to run out of ideas,
energy, and the ability to serve those that we lead. We simply “run out of
gas.”
Unfortunately,
there’s not enough emphasis in the business world about the need for leaders to
make time in their day for reflection. In fact, thanks to today’s accelerated
pace in the workplace, a greater focus is being put on a leader’s ability to
react fast to changes and making quick decisions for their organization. While
the ability to think quick on one’s feet is certainly a valuable trait for a
leader to demonstrate, it’s also important that leaders develop the habit of
putting aside time during their day to reflect not only on current decisions
their organization needs to make, but also to review past mistakes to see what
lessons their company can gain from that experience.
For
many leaders, the acknowledgement that slowing down for some part of the day is
necessary, desirable and valuable is in itself transformative. Even the very
practical leader will discover that regular time spent in reflection will bring
greater perspective and new levels of emotional clarity. This is the time to step back and take an
unhurried look at daily challenges, past “mis-takes” and future visions.
The
more you reflect, the more you realize that it comes naturally, and that
without it, you are not able to do your job. You will discover that we all
reflect, most of the time. By relearning how to use your reflecting skills as a
tool in your leaders toolbox, you can increase your ability to see possible
challenges early, and seek alternative solutions before you are forced into a
corner. You become pro-active.
Making
time to reflect on past decisions and mistakes, and allowing yourself the
opportunity to learn from it, is a critical step to continued growth and
development and your ability to effectively lead others.

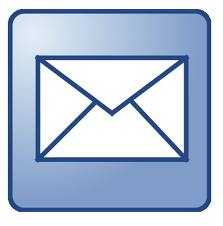




