Successful Lean transformation requires a deep understanding of the technical side of Lean supported by a culture that favors human development and broad employee engagement.
But which comes first: culture or tools...?
Come to the conference and you'll learn more.
I will be presenting at The Northeast Lean Conference in September in Worcester, MA on a topic I've covered here a few times.
SIPOC – The First Picture of Your Process
Wed Sep 20, 2017
10:00 AM - 10:50 AM
Description
Whenever you are planning to start some process improvement activity, it’s important to capture an easily communicated picture of the current process first. A SIPOC (Suppliers, Inputs, Process, Outputs, Customers) diagram identifies at a high level the potential gaps (deficiencies) between suppliers and process inputs and between output specifications and customers’ expectations, thus defining the scope for process improvement activities. In this interactive session, you’ll learn to understand the fundamentals of creating an SIPOC diagram, demonstrating how you can dissect a process and create a workable improvement plan that can be applied in your everyday workplace. Armed with a detailed and shared visual understanding of how work actually occurs, the organization can more easily identify project ideas for improvement.
Hope you can join me at this exceptional industry event for Lean practitioners in a few short weeks.

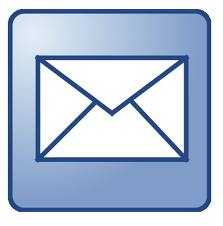




