Applying
Lean to office processes is an often misunderstood concept. Many efforts at
lean office often fall by the wayside since measuring improvement is nearly
impossible. It is important to analyze the office processes themselves to
determine how to apply lean appropriately. The best way to accomplish this is
to first understand how the seven wastes of manufacturing apply to office processes
to identify improvement opportunities.
To
identify and eliminate the waste that plagues your office, learn to identify
the 8 wastes in their manifestations.
Here is a list of the 8 common wastes of Lean, and some ideas about how
they manifest in the office environment.
Defects &
Inspection
This
is work that you thought was complete but requires to be touched again due to
not meeting the customer's needs. Inspection is the same as review and this is
in the flow because our internal customer doesn’t trust that we can deliver
what they want. This leads to more reworking of defects, but we have to fix the
process to produce a good product.
Examples:
•
Order
entry errors
•
Design
errors or engineering change orders
•
Invoice
errors
•
Lost
files or records
•
Bad
or Missing information
Over Production
This
is the act of producing more than what the customer wants instead of providing
what they need or actually paid for.
This is a fast way to lose customers as it requires more time and
resources, something that is in short supply.
Examples:
•
Producing
reports that no one reads or needs
•
Making
extra copies just-in-case
•
Producing
more to avoid set-ups
•
Entering
repetitive information on multiple documents
•
Memos
or email to everyone
Waiting
A
period of time delay spent while expecting something to happen or ready for
something to happen. Waiting waste is idle time created when material, information,
people or equipment is not ready.
Examples:
•
Waiting
for approvals or signatures
•
Attendees
not all on time for meeting
•
Slow
system response time
•
Delays
in receiving information
•
Printer
or computer break-down
Non-Utilized People
or Knowledge
People’s
skill, abilities, and knowledge are not effectively or appropriately used. This
happens frequently in large organizations where the skills and backgrounds of
everyone are not common knowledge. The biggest crime in this category is not
empowering or enabling the people most intimate with a process to improve the
process.
Examples:
•
Bypassing
procedures to hire a favorite candidate
•
Start
using software without prior training
•
Not
providing opportunity for professional development
•
Limited
authority and responsibility for basic tasks
•
Inadequate
business tools / training available
Transportation
This
is where you have to take the product you are working on and move it
somewhere. That act of moving does not
change fit, form, or function. We are
usually taking it to the boss to drop it off on their desk be reviewed, so we
can rework it later. I see a pattern
developing here.
Examples:
•
Moving
product in and out of storage
•
No
signs identifying areas or departments
•
Multiple
hand-offs or approvals
•
Bad
area layout
•
Excessive
filing of documents
Inventory
Inventory
is a common result of multi-tasking and otherwise un-balanced workloads. It can be found in e-mail or work order
in-boxes, to-do lists, product development pipelines, and resource assignment
charts. If a person has three tasks to
complete, it is guaranteed that two of them are waiting (in inventory) while
that person performs the third. If you
want to be able to see inventory like you do on the factory floor, you must
make the lists, in-boxes, resource assignments, and project pipelines visible
in your workspace.
Examples:
•
Excessive
office supplies
•
Files
piled up between desks
•
No
storage space because its filled with stuff not needed
•
Batch
processing transaction & reports
•
Obsolete
files or office equipment
•
No
sufficient cross-training
Motion
Excess
motion primarily refers to people having to walk to office equipment or (even
more importantly) having to walk to find people. Meetings are motion in the
sense that they are work without producing, unless a decision is made or
information is produced during the meeting. Motion shows up as people search
for files they can’t find, in phone calls to track down information, or from
unnecessary button clicks to get to the bottom of a work order to update the
to-do list.
Examples:
•
Looking
for items without a defined place
•
Searching
for files on computer
•
Employees
not working to a standard method
•
Poor
work area layout
•
Sorting
through materials
Excess Processing
Excess
processing often results from the creation of multiple versions of a piece of work
that now must be reconciled into the true work.
It shows up in additional signature approvals, data entry or data format
changes, frequently revising documents or information, or complex forms or
databases that require information to be entered repeatedly.
Examples:
•
Multiple
signatures
•
Unused
or unnecessary information collected
•
Re-entering
data
•
Different
software working on same document
•
Expediting
•
Unnecessary
or excessive reports

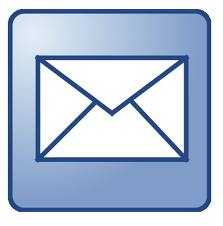





Very true. It is sometimes hard to be in an office and see the wastes but not empowered to make changes.
ReplyDeleteGood Job! Sometimes we get exemples from lean manufacturing and it is hard to translate them for an office or engineering development environment. Thanks!
ReplyDeleteI have recently changed careers to an office setting from manufacturing for 16 years. We were taught the principles of lean manufacturing. I am struggling to see the waste in the office, it is driving me insane! I tried to explain the waste and got shot down. Any suggestions to approach management on the ideas of lean?
ReplyDeleteFind a manager who will listen, if there are none, the place is probably not a long term solution for employment. Waste promotes a hidden agenda to fight change and in this day and age if you aren't changing or continuously improving you will fall to the wayside.
DeleteExcellent Information
ReplyDeleteI think it would be easy to convince people if the benefits are concrete and practical -- meaning the savings are there, verified by an independent department (accounting or purchasing). I believe in the reasonableness of man. No man in his right mind would reject such savings, if they're presented in clear terms.
ReplyDeleteThis is really great information. I never considered applying lean six sigma strategies outside of manufacturing, but I definitely have noticed these wastes in my office. I will use this information and start to make note of excessive waste to maximize office efficiency.
ReplyDelete