Many change cultures fail to achieve results simply because they try to do everything at once. A “can do” culture makes progress one step at a time and develops the ability to prioritize the order of these steps. Strategic priorities position the organization to achieve its goals. Only a few priorities should be central to all areas of the organization.
When your organization is undergoing change, consider altering its priorities. Changing priorities is a significant change, but it does not tamper with the personality or character of the organization, as long as any new priorities are aligned with its purpose and the philosophy.
Prioritizing is not an easy task. There seldom is an absolute right or wrong decision, but rather several options with advantages and disadvantages. Like many soft skills, it can be taught or grown through champions within the culture who have the training or natural abilities.
The ability to prioritize enables the ability to focus, but they are not completely identical. Once the priority is set, every member of the culture needs to be informed and directed toward the specific goal to achieve the focus necessary for meaningful improvement. Again, working on too much at once is the enemy of focus. The elephant must be divided into bite-sized pieces and everyone needs to be focused on the same bite at the same time.
From the individual perspective, focus is about concentrating attention. From an organizational perspective, focus is about centralizing the attention of the group through communication and collective problem solving. These abilities can be taught, but they often are more a matter of learning by doing rather than of formal education or training.
Strategic priorities are the values that guide how the purpose and the philosophy of the organization are put into practice. Priorities matter especially when changing the culture.

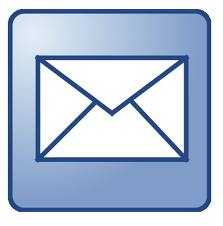




