Every year companies ratify and formally commit to their quality policies but are they more than words on paper. It should be part of the culture of the company. Employing quality methods and practices in everything you do provides a firm foundation for your business and can be a determining factor in your success.
To create a culture of quality, an organization must align its organizational processes with quality planning and desired outcomes. Quality leadership starts with the leaders who plant the seeds, create the environment for success, empower others and deploy quality throughout the organization.
Improving quality is about taking action to increase value to the customer by improving effectiveness and efficiency of processes and activities throughout the organization. Quality improvement places a stronger emphasis on leadership rather than management competencies and attributes. Leadership’s critical task is to integrate, institutionalize and internalize quality.
Successful implementation of quality improvement requires commitment, focus and patience, but the rewards are substantial. Beyond the obvious practical benefits, organizations become empowered to solve persistent process and performance challenges while raising the expectations they set for themselves. A quality organization understands that the realization of quality must be continually energized and regenerated.
As stated earlier, management commitment is vital to overcoming uncertainty, establishing credibility and providing the stability to allow change to gain a foothold in the organization. Senior managers must create and maintain buy-in for quality improvement at all levels of the organization. Leadership must manage the organization’s culture and be a visible advocate for quality--“talk the talk and walk the walk.”
Excellence in quality improves customer loyalty, elevates brand position, reduces cost, attracts new customers, and draws the best and brightest talent. A strong orientation for quality helps to achieve business goals. Achieving excellence in quality provides significant momentum for the business and is a source of pride for all employees. A comprehensive quality management system is a key attribute to the longevity and success of an organization.

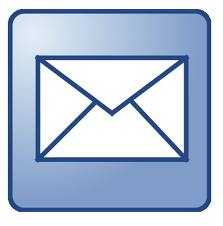




