Many of you know this time a year I spend a lot of time at an ice rink coaching hockey. It is a sport I have played all my life and coaching provides an opportunity for my kids and others to have the same experience (hopefully). As a coach you can’t help but feel a sense of instilling good behaviors in your players. While you might be teaching specific skills and helping them understand the strategies of the game I think the opportunities to teach life lessons are the most important.
In my experience I liken this to the way a Lean Sensei (champion, mentor, teacher) coaches continuous improvement thinking. They don’t focus on the tools necessarily but rather the approach or method of problem solving. It is this that provides a valuable foundation of Lean thinking from which you can address any situation.
On a long drive back from a game as the season is winding down I got to thinking about the lessons I hope my players take with them through life. Many of these lessons are the same that I and others try to instill in the organizations we work with. So in no particular order here are five lessons that apply to sports and Lean:
1. Never give up. Sports have lots of highs and lows throughout the game. Perseverance is necessary to turn a bad situation into a good situation. When your team is behind never give up or you will be defeated. Lots of teams come from behind to win.
Lean also needs perseverance to get you through the difficult bumps in the road along the way to improvement.
2. Practice. Practice. Practice. All sports teams practice in order to improve. The key to their practices is to focus on basic skills for game situations. This high speed sport is much about reading and reacting so you must practice with intensity if you want to play with intensity.
In your organization you may not necessarily call it practice but you certainly experiment. This experimentation is what prepares us to solve more and more complex problems.
3. The power of teamwork. Hockey is not an individual sport it requires every member of the team to play their part to win. It also requires everyone to be at their best. Open communication and chemistry are an essential part of teamwork.
We all have roles in our organizations but it is the power of teamwork that makes our endeavors successful. It takes everyone working together on a common goal to be successful in Lean.
4. The value of hard work and sacrifice. Undoubtedly it takes a lot of hard work and sacrifice along the way to get to the elite levels of the game. But this makes winning so much sweeter in the end.
Lean takes lots of hard work as well but it makes wins you get much more pleasurable. It is this hard work that creates customer value and makes your organization competitive in the market place.
5. Winning requires a positive attitude. There are a lot of things out of our control and adversity is part of the challenge but how we react is up to us. The right attitude can keep you moving forward. Never dwell on what you did wrong but what you need to do better for the next game.
Lean requires a willingness to try something new to improve our workplace. Fix what bugs us. Make work easier.
I am reminded of a great quote from Mark Messier at the 2007 Hockey Hall of Fame Induction Ceremony:
"For all of us that have children in minor hockey, it's not about becoming a professional athlete, it's about the journey and about what you learn along the way and the life lessons that you get from playing an incredible game."
Even if you’re not a hockey fan like me, I hope you’re able to take some of these life lessons from ice hockey and apply them to your experiences. I think these are lessons we can all use especially in a continuous improvement environment. What do you think?

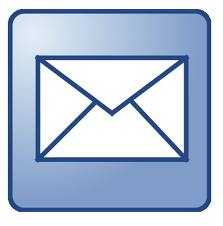





Tim,
ReplyDeleteThose are all great lessons that can be applied by all of us. Thanks for sharing.
Chris