Lean thinking has been around since the early 90’s. Despite this fact true Lean thinking still evades many. There continues to be stories in the news about company’s misfortunes mistakenly attributed to Lean implementations. If we truly want to improve our businesses we must dispel these myths so the real power and benefits of Lean can be known.
Here are 5 big misconceptions about Lean and my rebuttal:
Lean is only about cost reduction.
First and foremost, Lean is about value — a bigger and more inclusive concept than mere cost. That is antithetical to genuine Lean process, the simplest definition of which is the continual pursuit, identification, and removal of waste in product and process. Waste is anything that does not contribute value — anything the customer will not willingly pay for. Traditional cost cutting occurs in silos, without regard to who is affected upstream and downstream. These impacts cannot just negate the initial cost reduction from the unilateral approach, but exceed them. Lean examines each process, internal and external, finding and removing the waste, and reducing cost while maintaining the health of all constituents.
Lean makes employees feel like robots.
People are often concerned that Lean efforts, including standardized work, will turn them into unthinking robots. Many Lean methods are used so that abnormalities are clearly visible and therefore can be reacted to. It is not about mindless conformity. Lean creates a baseline so improvement can occur by freeing up mental capacity from doing the routine in order to think about how the process could work better. A truly Lean culture respects people and engages them in continuous improvement.
Lean is just about applying tools.
This is a myth perpetuated by less than knowledgeable leaders. Most companies miss the point that 90% of Lean is about people and culture change and only 10% is about the tools. They expect Lean to be the “silver bullet”, which, even if it does not solve all their problems, will at least aid in short-term gains. There are thousands of Lean tools, because each problem requires its own unique tool to help solve it. People are needed to solve problems. Tools don’t apply themselves. Basically, leaders have to learn to think differently and see their customers and business differently, that’s people development, not tools development.
Lean is something you do in addition.
Lean is not about the destination but the direction or path you take toward this idealistic place. Lean is not something you check off your "To Do List". It is about the constant, persistent, even relentless pursuit of improving your current situation. Usually, it means doing something you haven’t done before because your old habits will not work in your new system. Lean is not technique you apply to your business system but rather a methodology that replaces your business system.
Lean means no inventory.
Lean doesn’t mean ZERO inventory. It means the right inventory at the right time at the right quantities and in the right place. Every company needs buffers, but they must be well planned and controlled. As anybody who has spent some time in a manufacturing plant will tell you, operating without buffers is a sure recipe for disaster. Low inventories are commonly linked to Lean because many organizations are able to reduce inventory levels due to practicing Lean Thinking. But "true" Lean Thinkers understand lower inventories are a resultant of a process improvement not a solution to a problem.
Unfortunately, there are many more myths regarding Lean thinking and methodology. As a Lean practitioner and voice in the community I feel a sense of importance to dispute these myths so that others can learn what Lean is really all about. Please, help contribute to this mission by sharing yours thoughts on Lean myths below.

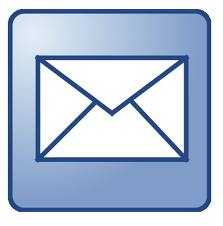





Great post. Another myth I hear a lot is that there is an upfront cost to adopting Lean.
ReplyDeleteI love last point "Lean doesn’t mean ZERO inventory." Have seen lot of well-intended persons not understanding the unit of work, which could be one-piece, one-bundle, one-pack or even one-batch to name some.
ReplyDeleteI still believe the biggest hurdle to Lean is a lack of understanding. You would think we the amount of literature on this subject it wouldn't be but nonetheless it is. Too many try to copy instead of understanding Lean and their own situation. Hopefully we can continue to educate other on "Real Lean" as Bob Emiliani says.
Delete