Click this link for A Lean Journey's Facebook Page Notes Feed.
Here is the next addition of tips from the Facebook page:
Lean
Tip #841 – Ensure a Penalty-Free Exchange of Ideas
Ensuring
a penalty-free exchange of ideas is beneficial to both the giver and the
receiver of new ideas and approaches and will ensure a safe two way exchange of
thoughts and ideas.
Lean
Tip #842 – Use A Consistent Approach For Projects
A
consistent and structured approach for project identification and execution
will provide the organization with the ability to identify, select, and manage
continuous improvement projects. It should also provide post-closing process
steps to continually refine the improvement project methodology and to act upon
the lessons learn from the project effort.
Lean
Tip #843 – Measure and Monitor Key Performance Indicators
It
is not possible to improve what is not measured. Determine in advance the
approach and techniques to be used in measurements. Scorecards can be useful to
monitor the key performance indicators of processes that support capability and
performance.
Lean
Tip #844 – Ensure Regular Communications to Foster Collaborative Interactions
Ensure
regular communications to foster collaborative interactions among leaders,
stakeholders, and practitioners at all levels.
Where needed, schedule face to face meetings and where not needed, use
the communication and collaboration tools and capabilities of the enterprise to
keep all members updated and involved.
Lean
Tip #845 – Establish Core Values that Comprise The Continuous Improvement
Culture
Establish
the core values that comprise the continuous improvement culture such as a
focus on supporting the customer, teamwork throughout the extended enterprise,
receptivity to evolving continuous improvement concepts and tools. These core
values will create a sense of belonging and a common vision for all involved.
Lean
Tip #846 - Identify an Internal Change Agent and Gain Commitment From Leadership
The
successful implementation of a lean manufacturing program requires the
engagement of company leadership to ensure lean doesn't become the company's
latest “flavor of the month” program. I recommend identifying an internal
“change agent” who will have overall responsibility for driving your lean
transformation. Change won't come easy, so this person must be respected, have
good communication skills and the ability to turn pushback into idea
generation.
Lean
Tip #847 - Turn Employees Into Problem Solvers and Improvement Specialists
The
most important aspect of lean is to involve employees in developing lean
processes. Many times companies create a culture in which the employees don't
make the decisions, management does. Then when problems occur, employees are
unable to diagnose or solve problems without involving a supervisor. lean
reverses that by revolving around employees and looking to them as the
improvement specialists.
Lean
Tip #848 - Share As Much As You Can
Shared
information will help to stop silos emerging and can help to manage the
‘collective expectation’. Furthermore, regular communications and clear
messaging explains the benefits to the wider team and will be widely welcomed.
Lean
Tip #849 - Devolve Responsibility To Those At The Gemba
Those
on the shop floor are vital in that they will be able to spot imperfections and
inefficiency. Don’t just involve them in
discussion, but make them experts and give them responsibility.
Lean
Tip #850 – Instill Confidence In Your Employees To Suggest Improvements
Instill
confidence in your employees so they will feel free to suggest improvements. In
the firelight, our cave dwellers could assess and improve their procedures. In
one set of drawings, the hunters stand in front of the stampeding herd. Where
do you think we would be today if people had not felt free to suggest
improvements?
Lean
Tip #851 - Empower Them to Think Differently
While
it’s important to set clear goals and responsibilities, the key to having a
successful business and engaged workforce is to empower all your employees to
make decisions on their own. Make sure employees are comfortable and confident
asking questions, bringing forward new ideas and even taking a different
approach that may fail. Out of that failure will come knowledge and longer-term
success.
Lean
Tip #852 - Create Opportunities for Employees to Shine
While
every company is pleased to have natural-born leaders, others may need a bit
more prodding. Empower those employees by providing them with a bit more
freedom to pursue to their passions. Then give them the opportunity to
demonstrate their work to other employees.
Lean
Tip #853 - Listen to Learn and Ask Questions to Provide Guidance
Provide
a space in which people will communicate by listening to them and asking them
questions. Guide by asking questions, not by telling grown up people what to
do. People generally know the right answers if they have the opportunity to
produce them. When an employee brings you a problem to solve, ask, "what
do you think you should do to solve this problem?" Or, ask, "what
action steps do you recommend?" Employees can demonstrate what they know
and grow in the process. Eventually, you will feel comfortable telling the
employee that he or she need not ask you about similar situations. You trust
their judgment.
Lean
Tip #854 - Promote Employee Education.
Provide
a means for employees to get whatever training is necessary to their optimal
performance so that they can truly master their job responsibilities. Also,
show that you are invested in their professional success by arranging for them
to attend career development seminars and courses. Not only does this provide
for employee empowerment, but it is a great way to gain employee loyalty and
improve employee performance.
Lean
Tip #855 - Really Listen to What Your Employees are Telling You.
It
is hard to know what your employees want and need if you do not truly hear and
understand what they are saying. Set aside a designated time to meet one-on-one
with each employee at least once a month. During your meeting, actively take
notes on what your employee is saying and asking. Your notes will help you to
listen more effectively.

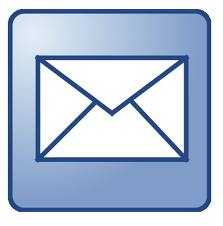





No comments:
Post a Comment