The
terms “quality assurance” and “quality control” are often used interchangeably
to refer to ways of ensuring the quality of a service or product. The terms,
however, have different meanings.
Control:
An evaluation to indicate needed corrective responses; the act of guiding a
process in which variability is attributable to a constant system of chance
causes.
Quality
Control: The observation techniques and activities used to fulfill requirements
for quality.
Assurance:
The act of giving confidence, the state of being certain or the act of making
certain.
Quality
Assurance: The planned and systematic activities implemented in a quality
system so that quality requirements for a product or service will be fulfilled.
At
its simplest, quality control is inspecting, testing or checking something
(service or product) to make sure it's OK.
The intent is to identify anything that isn't OK, and either fix it or
eliminate it, to make sure it conforms to the specifications, and
has/does/functions as required. Quality
control is typically done at the end of the line, before it 'goes out the
door'. If the something isn't OK, this is called 'nonconformity' or a
nonconforming service/product.
Quality
control does not ensure quality, it only finds instances where quality is
missing. Obviously it's better than
nothing, but it has its limitations. The
most important of these is that you only find out that things aren't OK at the
end of the process.
Quality
assurance developed from the realization that quality could be improved by
looking 'further up the line'. Quality
assurance activities are determined before production work begins and these
activities are performed while the product is being developed. It is aimed at
preventing nonconformities/defects.
Quality
assurance focuses on processes and their continuous improvement. Its goal is to
reduce variance in processes in order to predict the quality of an output
(final or interim product), gather best practices for the company, reduce cost,
and reduce time to market. Quality assurance is strongly linked to innovation and
creativity. Quality Assurance neither imposes nor defines processes for other
people, but it provides advice and support to the process owner, which leads to
the ability to measure success and make decisions based on facts.
Quality
control is concerned with examining the product or service — the end result
and quality assurance is concerned with examining the process that leads to the
end result. A company should use quality assurance to ensure that a product is
manufactured in the right way, thereby reducing or eliminating potential
problems with the quality of the final product.

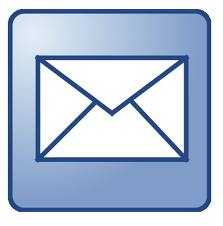





Tim -
ReplyDeleteThat is a great post. As soon as I read your point that they are different, I thought "they certainly are". I don't think anyone would disagree with your definitions. I appreciate the post because it is something we don't call out and make an effort to remember. It may seem like it is an obvious difference but I never stop and think about it.
Thanks.
Like most things I write about this was based on experience. While obvious on paper it becomes less so in reality for many companies. Clearly, our efforts need to be on prevention rather than detection.
DeleteThis post so nice. Thank you for sharing.
ReplyDelete