Companies
with poor management practices typically have employees who are disengaged. While
a disengaged workforce is a symptom of substandard leadership, just what
constitutes bad management? Here are a few problematic practices and signs I believe
should be axed:
1.
Bad Communication
Few
things cause employees to tune out faster than a management team that keeps the
company's future direction to itself. Successful Lean leaders see the larger picture
and will share the vision.
2.
Team-Building that Isn't
Fostering
a connected team is an important practice, but before implementing group events
and activities, be sure members of your team won't feel left out. Getting to know your
team members is generally an effective way to build collaboration and a sense
of joint purpose.
3.
Little or No Training
According
to a 2011 report from Accenture, 55% of workers in the U.S. say they are under
pressure to develop new skills, but only 21% say their companies have provided
training to learn those new skills within the last five years. Training is a
lever that changes the rate of improvement you can achieve.
4.
Preventing Follow-Through
Most
employees like to feel their work has meaning. If they don't get this kind of
satisfaction, they lose motivation, according to a number of research studies.
One sure way to demean an employee's work is to move them off a project before
it's completed. Lean leaders must follow-up on employee ideas.
5.
Ruling by Fear
Managers
who rule through rigid control, negativity, and a climate of anxiety and fear
don’t trust that they can get things done any other way. Of course, it
backfires in the end because fearful employees won’t bring up new ideas for
fear of being attacked and won’t be honest about problems. Moreover, very few
great people with options are going to want to work for a fear-based manager.
6.
A Failure to Develop Others
Leaders
who are not concerned about helping their direct reports develop and are not
seen as coaches or mentors are highly likely to fail. Primarily focused on
themselves, they are not concerned about the longer-term success of their
employees or their department.
7.
Failure to Improve and Learn from Mistakes
Arrogance
and complacency combine in the poorest leaders as they rise, causing them to
come to the dangerous conclusion that they’ve reached a stage in their careers
where development is no longer required. Closely connected to this failing is
an inability to learn from mistakes, leaving these unfortunates to repeat the
same ones over and over.
8.
Failure to Walk the Talk
Saying
one thing and doing another is the fastest way to lose the trust of all your
colleagues. The worst offenders here also pose a wider threat as dangerous role
models — creating the risk that their organizations will degenerate if others
behave as they do.
9.
Lack of Data
Many
managers rely on gut instinct to make important decisions, which often leads to
poor results. On the contrary, when managers insist on incorporating facts and
evidence, gathered
from direct observation at the source they make better choices and their
companies benefit. Lean
companies however strive to empower their employees to make decisions at all
levels through access to data, knowledge of evaluation methods, and defined
standard processes.
10.
You Always Have Emergencies
Business
is sometimes unpredictable. But the fact that things are unpredictable is,
well, predictable. As a Lean manager, it's your job to assess the situation and
plan in advance. Occasional emergencies are understandable, but constant ones
mean that you're not doing what you need to do. Sometimes that involves pushing
back against your superiors and protecting your people. It means scheduling
according to actual needs, and if you don't have the budget for that it often
means changing the definition of need.

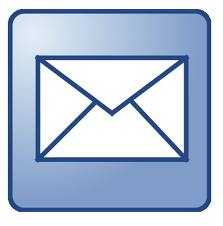





Hummmm I think I know this guy......
ReplyDeleteUnfortunately, I think we all have experienced someone like this in our career. Hopefully, this can help us shape better more engaging leaders.
Delete“10 signs to non-learn manager” I read your thoughts it’s very informative. These steps are very helpful to improve workplace environment. As I am a manager. I must follow some rules. Less and bad communication increases your work pressure so never stop communication.
ReplyDelete