Some may say that it’s impossible to eliminate mistakes. And they are right; it is, most of the time. But, to be honest, they are missing the point.
Poka
yoke, or mistake proofing, describes any behavior changing constraint that is
built into a process to prevent an incorrect operation or act occurring. The three aims of mistake proofing are:
- To reduce the risk of mistakes or
errors arising.
- To minimize the effort required
to perform activities.
- To detect errors prior to them
impacting on people, materials, or equipment.
Ideally,
poka-yoke ensures that proper conditions exist before actually executing a
process step, preventing defects from occurring in the first place. Where this
is not possible, poka-yoke performs a detective function, eliminating defects
in the process as early as possible.
This
can be achieved using three rule. Following are three rules of poka yoke
- Make it impossible to get it
wrong (Occurrence)
- Make it impossible to pass the
defect onto the customer (Severity)
- Make it blatantly obvious that
there is a defect (Detection)
In
our normal lives we are all familiar with many different mistake-proofing
concepts, such as windows that don’t open fully in order to prevent people
falling out, self-closing fire doors, lights that turn themselves off when they
detect no one is there, and so on. You will also have seen warning instructions
and traffic lights, as well as having read work instructions, all of which aim
to reduce the risk of error. However, you will also notice that some of these
are more effective than others. For example, the windows that don’t open on the
15th floor of a hotel to prevent you falling out are likely to be
more effective than leaving the windows able to open fully and providing an
instruction pamphlet in one of the drawers that tells you to be safe when
opening the windows. This shows there is a hierarchy of mistake proofing
concepts, with a decreasing level of effectiveness.
The
five levels of the hierarchy of mistake proofing are shown below.
- Eliminate – the most effective
but also normally the most costly level involves eliminating the source of
risk completely. In reality, it is very difficult to completely remove
risk.
- Redesign – if you can’t eliminate
the risk then you might want to try to replace it with a less risky
process.
- Reduce – when it is not possible
to redesign the problem you need to think about reduction techniques.
- Detect – here we are no longer
trying to prevent mistakes: we are trying to detect they have occurred.
- Mitigate – at this lowest level
we are simply trying to reduce the damage caused by the mistake arising.
Some
common examples of mistake proofing that most people should be aware of – and
the levels they represent in the mistake proofing hierarchy:
- Hard hats - mitigate
- Drain hole at the top of a sink
to prevent it overflowing - mitigate
- Fuel low warning lights on cars –
detect
- Blood pressure monitoring
equipment - detect
- Safety glasses – reduce
- Standard operating instructions –
reduce
- Filing cabinets that won’t allow
you to open more than one drawer at a time – redesign
- Garage door sensors that detect
an obstruction – redesign
- Irons that turn off automatically
– redesign
The
guiding principles of mistake proofing should be as follows:
- People are fallible and even the
best make mistakes.
- Errors are inevitable.
- Errors can be eliminated.
- Error-likely situations are
predictable, manageable, and preventable!
- Events can be avoided by
understanding the reasons mistakes occur and applying the lessons learned
from past events.
- Defects are preventable and zero
defects can be achieved.

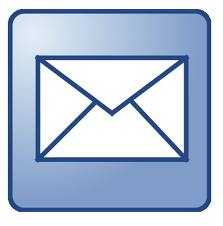





Is the hierarchy of mistake proofing you're presenting here something you came up with or referenced from something else? I've just noticed that it's very similar to the Hierarchy of Hazard Control (http://en.wikipedia.org/wiki/Hierarchy_of_hazard_control) and I was wondering if there's similar heritage
ReplyDeleteJason the hierarchy of mistake proofing is not my own. The exact source escapes me (course, book, webinar, etc). They are similar to those of the hierarchy of Hazard control. Not surprising I guess given the subjects. I imagine this thinking comes for Henry Ford and was later refined at Toyota by Shigeo Shingo.
DeleteJohn Grout's website (www.mistakeproofing.com) is always a resource I have found value regarding the subject.