To
ensure the success of your corporation you must ensure that your company is
operationally disciplined. Operational discipline must be part of your
company's culture.
Operational
discipline is defined as the deeply rooted dedication and commitment by every
member of an organization to carry out each task, the right way, each time. ‘‘Discipline’’
in this context
does not refer to punishment, but to doing things in a way that results in
positive benefits. Operational discipline reflects the strength of an organization’s Lean
culture in making systems effective and in providing tangible result. In
addition, a high level of operational discipline typically contributes to
improved business performance through higher productivity, higher quality,
reduced waste,
and lower costs.
Operational
discipline is the willingness to create and follow processes/rules and hold
people accountable for performing them. In Lean speak, it includes elements of Plan-Do-Check-Act
(PDCA). There are 3 operational
discipline techniques that you can use to produce higher quality.
Standard Work
(Plan-Do)
Standard
work is a written description of how a process should be done. It guides
consistent execution. It
is the most effective combination (method) of manpower, materials and machinery.
Andon (Check-Act)
Andons
are audible, or more commonly visual, signals that something has happened. The aim is that andons quickly alert
managerial and technical staff to a problem having arisen so that they can get
to the source of the problem and begin to investigate it.
Audit (Check-Act)
The
final step in the process is setting up a quick audit process to make certain
your rules are being followed and your process is staying in good shape. Use
audits to not only sustain the improvements from Kaizen, but also expose new
problems and resolve them with your employees' involvement and input. In the
beginning, the audits may need to be more frequent to force the discipline to
adhere.
In
an organization where a strong Operational Discipline culture exists, there
will be a “deeply rooted dedication and commitment by every member of an
organization to carry out each task – “the right way, every time.” Through standard
work, each process is defined and performed the same way every time. Implementation
of signals will alert you of problems early which improves quality and provides
a foundation for continuous improvement. Auditing ensures you do what you say
you will do. Create a culture that is operationally disciplined and you will
find improved business results, better quality, and less waste.

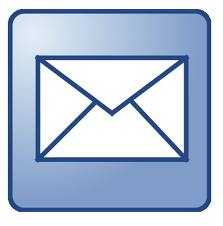





No comments:
Post a Comment