"People tend to think that they need a process
for everything, and once in a while you hear 'We're going to dummy-proof it.'
But if you dummy-proof the process, you only get dummies to work there." — Reed Hastings, CEO Netflix
People
are often concerned that Lean efforts, including standardized work, will turn
them into unthinking robots. Many Lean methods are used so that abnormalities
are clearly visible and therefore can be reacted to. It is not about mindless
conformity. Lean creates a baseline so improvement can occur by freeing up mental
capacity from doing the routine in order to think about how the process could
work better.
A
common myth about standardized work is that many think of a rigid work
environment where workers aren’t required to think. This is totally the
opposite. Operators are part of the creation of the work standard and then are
challenged to improve these methods. The standard creates a baseline by which
improvement can be measured. Ideas should be discussed with group leaders and
considered depending upon the consensus and buy-in from other members and
shifts. Once consensus is reached then experimentation can be done to determine
the effectiveness of the improvement. If it is deemed an effective change then
the standardized work can modified and everyone trained in the new method.
The
worst kind of waste is the lack of employee involvement and creativity. Lean
doesn’t work unless everyone is involved and has input. We must involve
employees in the continuous improvement process because the people actually
carrying out the job know how to do that job better. A truly Lean culture
respects people and engages them in continuous improvement.

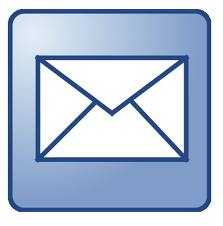




Tim,
ReplyDeletegreat thread. what is missed by most folks is the effect that properly prepared standardized work has on intrinsic motivation. if the workers are properly involved in the creation of and teaching of the standardized methods it triggers all five of the intrinsic motivators and they love it....that is if it properly done through an engaged and properly involved work force. management cannot abdicate their role and just tell the worker to "do it", nor can they prepare the work and then just tell the worker to comply. Neither a command and control nor a laissez-faire management style will work......
Lonnie Wilson
law@qc-ep.com
I still cringe at the term "dummy proof" or "idiot proof."
ReplyDeleteIt reminds me of the old Toyota story where Ohno (or Shingo) used the term "baka yoke" or something which meant "fool proof." An employee got upset and ran off saying, "I am not a fool."
So the term "poka yoke" came into use - mistake proofing or error proofing. We're protecting against errors and focusing on the process, not the person. We're also protecting people from caught in the middle of an error caused by a bad process. That's especially true in healthcare... we have to not just protect patients but we also have to protect healthcare professionals from having their careers ruined because they unjustly get blamed for something.
Mark