Yokoten is a Japanese term that can be roughly translated as "across everywhere." In the Japanese lean system, it is used to mean "best practice sharing." Yokoten, the term Toyota adopted to capture the idea of horizontal transfer of information and knowledge across an organization. Yokoten encourages sharing of data across the organization.
To Yokoten is to spread across or propagate. This is like the multiplying of saplings in nature from a large tree to many new trees. The new trees will grow in the proper soil and weather conditions. However, each new tree will grow and adapt differently to their unique environment. They are not clones, but take on a life of their own. This is true of Yokoten as well. It is not just a “go and see and then copy.”
Yokoten is horizontal, or more peer-to-peer, with the expectation that people go see for themselves and learn how another area did kaizen. In Yokoten at Toyota there is an expectation that copying a good idea will be followed by some added kaizen to that idea.
Inside of organizations, there is so much untapped knowledge. To combat this, over the past two decades, companies have invested millions of dollars in knowledge management systems. The objective has been to capture the company’s knowledge. Yokoten is a form of knowledge management. It encompasses the methods of documenting and distributing knowledge about what works and what doesn't. As a knowledge management device, Yokoten makes knowledge organizational, not individual. Yokoten is a two-way street, requiring proactive effort from both those acquiring and developing the knowledge and those who could benefit from greater understanding of the requirements for success.
If others are doing well, people tend to be interested in what they are doing and how they're doing it, so that they, too, can be successful. Sharing best practices is a key part attributing to the success of any organization. Similar to the old saying, "Learn from other's mistakes," it's important to learn from individual experiences, but it's much easier and more effective to learn from the experiences, mistakes and successes of others.
Much of best practice knowledge is tacit - held in people's heads and not always easy to document. Therefore, most best practice programs combine two key elements: explicit knowledge such as a best practices database (connecting people with information), and methods for sharing tacit knowledge such as communities of practice (connecting people with people). Communities of practice are groups of people who share a concern or a passion for something they do and learn how to do it better as they interact regularly. These two approaches are complementary. A database can provide enough information for a potential user of the best practice to find it and decide if it is worth pursuing further. However, the best way of sharing best practices is 'on the job' and so communities and personal contact with others who have used the best practice is key.
Yokoten is an essential part of long-term success in a lean culture, but can also have a big impact on short-term results. Yokoten is a success multiplier. Senior leaders must actively go see, recognize good work and require others to go see. Management must organize presentations of successful kaizen projects and invite colleagues to attend and learn. Team and department leaders must actively engage members in studying kaizen examples, motivating them to start kaizen on their own. Project leaders and continuous improvement professionals must put Yokoten on their checklists and follow up rigorously.
Regardless of your path on the Lean journey, focusing on the accumulation and transfer of knowledge and learnings as embodied in the concept of Yokoten can have a tremendous impact on the overall results and success of the Lean programs.

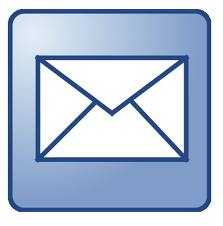





Awesome article, Time! I've been facilitating a lean process improvement initiative in our multi-facility healthcare organization. The go-and-see, peer-to-peer learning can be powerful when teams can get past thinking in silos. Teams reflect the attitude of their site leaders when it comes to humble inquiry and a shared desire to drive excellence for the entire enterprise, not just the local site. Thank you for the linkage with communities of practice too!
ReplyDelete