Lean Manufacturing has been taught from practitioner to practitioner and company to company for decades. This learning and reciprocal sharing of best practices is what helps us all improve.
A network of like-minded professionals creates an opportunity for those that practice Lean, Six Sigma and other improvement philosophies to share their knowledge; and for those that are considering the methodologies to learn through questioning and relationships with practitioners. Local groups that share your interest in a particular topic, offer a great forum to learn and share information for little or no cost. Special interest groups within these groups can offer further topic specialization and can be a tremendous way to learn or be mentored.
Finding a network near you doesn’t have to be difficult. Many professional associations like the Association for Manufacturing Excellence (AME), American Society of Quality (ASQ), and many others offer these networks. Local MEP and consultants also have a good network of connections that can help. Start by finding those networks near you and ask how you can get involved.
Now, when you are ready to visit a company willing to share it is not enough to just show up. You should go prepared to answer one of your problems. If you visit with the goal of finding a solution to a problem at your company you will be more apt to find it. Copying solutions don’t work but can help you learn a better way. Remember to “adopt then adapt” when implementing solutions. The reverse often results in a failure to implement.
Hosting a visit is equally valuable. Here are some tips I’ve learned from hosting:
Set and meet expectations. Before the day arrives, understand what the visitors want to see. Suggest what might be the best way to experience your program. Be clear about the time commitment.
Seek feedback. Using something like the “3 idea form” ask visitors to record 3 good things they will take back with them and 3 opportunities for improvement for the host site.
Allow for follow-up. Make connects, share contact info, and create an opportunity for visitors to follow-up. Inherently, once you return home to implement something you might have seen you find more questions and it can be helpful to have someone to follow-up with.
Visiting a company or hosting a visit can be a great way recognizing your achievements. It also helps reinforce your pursuit of Lean by sharing your journey with others who are on the same journey. Networking supports the continuous learning cycle we all need to feed our improvements.

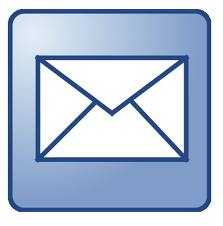




