The goal of Meet-up is provide you an opportunity to meet some other influential voices in the Lean community. I will ask these authors a series of questions:
Who are you and what do you do?
Jon Miller of Kaizen Institute. I try to help people and organizations remove barriers so they can achieve their potential.
How and when did you learn Lean?
I spent 8 years working as a Japanese-English interpreter for consultants from the Shingijutsu group. This took me around the world where these sensei were using kaizen events as a way to help companies solve problems and build a semblance of TPS. During these years I learned PDCA, how to make kaizen events work, and various TPS subsystems and improvement tools. I also learned that you can’t string together kaizen events and expect a lasting change. That inspired me to move into the consulting world in 1998. This allowed me to try out kaizen and Lean without having grey hair or a Japanese face. That’s when I really started learning the importance of the organizational and leadership elements of kaizen. Since the year 2000 we’ve organized more than 120 study missions to Japan and these were always opportunities to either firm up what I knew or shake it up and reframe it. What I still haven’t learned is how to make Lean succeed in social and business environments that lacking long-term thinking, basic fairness in compensation systems and a constancy in leadership purpose.
How and why did you start blogging or writing about Lean?
I started blogging about lean for purely mercenary reasons. A company advising us about internet marketing recommended that we start a blog to increase website traffic. At some point after 1 or 2 years blogging became a lot more widespread with other Lean bloggers joining in. Soon there were quite a few people reading and getting value from the blog. This gave me a sense of responsibility to put good quality information out there since there was and continues to be so much misinformation about Lean.
What does Lean mean to you?
At a deeper level it’s a very optimistic way of looking at the world and seeing that all of our problems are solvable. There is enough to go around. We can do more with less. People working together will find a way. This is necessary since a Lean person has to face the brutal reality of a staggering amount of waste in every industry and sector, behaviors contrary to Lean and so forth. At a superficial level, Lean is an annoyance. The term Lean is a small subset of the work we need to be doing, science in service of society in the broadest sense. Lean is an easy bundle of systems, tools, ideas, shorthand for getting started with improvement, but too often people aren’t curious enough to delve deeper so the new “Lean thing” that gets popularized is another bastardized version of something that is already ill-defined. At an extremely practical level, Lean is a livelihood and a profession. Here I am having dedicated 20 years to Lean, so I feel grateful to Lean regardless of the term’s limitations, and a sense of responsibility to make sure Lean grows up to achieve its full potential.
What is the biggest myth or misconception of Lean?
The misconception is that we can draw boundaries around a few observable things and label it Lean. The orthodox definitions of Lean are criminally inadequate. Elimination of waste, variation and overburden; customer focus, map value, flow, pull, pursue perfection; continuous improvement and respect for people, etc. All of these are important and practicing Lean can do us a world of good but until we look at Lean with an inclusive and truly long-term view of societal values, industrial policy, economics, education, etc. it will always be an exercise in rework.
What is your current Lean passion, project, or initiative?
I’m trying to do less. It’s a huge challenge.

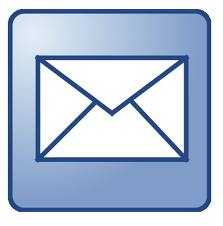





Tim, Thanks for sharing this interview.
ReplyDeleteJon, I really like your observation about "long-term thinking, basic fairness in compensation systems and a constancy in leadership purpose."
It has taken me a long while to realize whatever great thing a team might produce, in terms of culture and attitude, it can not be sustained without a devoted leader who will put himself in a position to continually learn by experimenting, doing, and reflecting (PDCA).
It is of little affect to "bring in the lean guy" and "have him lean out this and that" if there is not understanding by top management. Certain types of managers find little value in the gold that was dug up by someone else, and it will most likely be squandered or frittered away if they do not posses the traits you described.
Regards,
Robert Neel West