"Value your listening and reading time at roughly ten times your talking time. This will assure you that you are on a course of continuous learning and self-improvement." — Gerald McGinnis, President and CEO of Respironics, Inc.
Learning needs to become part of your daily routine. You are most likely to succeed if you consistently pursue a learning activity each day. Even five minutes a day can make a tremendous difference.
So how do you make learning continuously part of job? Here are six ways to get started today:
1. Pursue ways to develop and apply specific skills. The most effective way to develop your skills it to make it part of your daily routine. Each day, identify where you can practice new skills and behaviors. Compile a list of people who can support your development. Observe people who are skilled in the areas you are trying to improve.
2. Get the most out of readings and seminars. When you are reading or are attending a seminar, take notes. Search for one insight or application in everything you read. Decide what you will do differently.
3. Involve others in your development efforts. Effective development rarely happens in isolation. Instead, successful learning occurs through a continuous process of feedback and support. Learn from people outside of work and realize that no single person will fill all your needs. Use resources available through professional associations, Web sites, blogs, and so forth.
4. View mistakes as learning opportunities. Mistakes are a problem if you repeat them or don't learn from them. When you make a mistake, ask yourself what you can learn from it.
5. Stay informed about industry practices. Industry practices and standards change so you need to keep up-to-date on developments. Visit other companies and talk with their employees. Attend industry or professional meetings, conferences, seminars, webinars, and other educational events. Join a group of professionals who get together to discuss issues of common interest.
6. Seek out and learn from others who are different from you. Getting input and advice from a wide range of people will provide you with new ideas. Develop a habit of identifying what you can learn from each person you meet. Realize that to keep learning, you need to put yourself into unfamiliar situations. Network with others to learn needed information.
Everything can contribute to our experience of learning. But as you may realize, learning is incomplete if we don't listen to the voices of those whose background and experiences are different from our own. Part of our learning continuously is opening our minds and hearts to those who propose a different way.

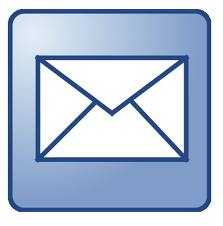




