Click this link for A Lean Journey's Facebook Page Notes Feed.
Here is the next addition of tips from the Facebook page:
Lean Tip #526 - Create opportunities to showcase your employees.
"Billboard" employees to your own supervisors and to others in upper management as well as to those outside your department or division. Some managers erroneously think that if they give workers credit, upper management will question the manager's own performance. But managers who fall into the trap of competing with the employees they supervise usually stall their own careers.
"Billboard" employees to your own supervisors and to others in upper management as well as to those outside your department or division. Some managers erroneously think that if they give workers credit, upper management will question the manager's own performance. But managers who fall into the trap of competing with the employees they supervise usually stall their own careers.
Lean Tip #527 - Add interest and challenge to workers' day-to-day routines by implementing job rotation.
Job rotation simply involves placing employees into jobs of equal value that they may have expressed an interest in or that you expect, based on their skill strengths, they may do well in. Some organizations encourage employees to initiate job rotation through a formal process, thereby increasing job skill levels as well as motivation.
Lean Tip #528 - Provide employees with responsibility and authority to successfully accomplish assignments.
Today, progressive companies utilize the skills and talents of their employees by assigning them to cross-functional or self-directed work teams. Employees not only perform their own specific job functions by have a team identity as well. Team members are responsible and accountable to the team for achieving its goal, implementing processes, and sharing the recognition for its results.
Lean Tip #529 - Provide assistance to employees without taking away responsibility to complete the job.
Clearly define your role and avoid the temptation to do the job yourself when employees find themselves in hot water. Let employees go it on their own and face those gut-wrenching challenges.
Lean Tip #530 - Find ways to foster employee self-esteem and self-confidence.
Although important, managers and supervisors must do more than give praise and provide meaningful work. To empower employees, supervisors must continually build employee self-esteem.
Although important, managers and supervisors must do more than give praise and provide meaningful work. To empower employees, supervisors must continually build employee self-esteem.
Lean Tip #531 – Limiting overproduction helps make the process Lean but also a lot more Green.
Identify areas of overproduction and root causes of waste in the current manufacturing system and find ways to reduce or eliminate them in the future. Some raw materials can be recycled meaning your carbon footprint will be reduced, however energy consumption will increase and the amount of unnecessary products needing disposal is a distinct possibility.
Identify areas of overproduction and root causes of waste in the current manufacturing system and find ways to reduce or eliminate them in the future. Some raw materials can be recycled meaning your carbon footprint will be reduced, however energy consumption will increase and the amount of unnecessary products needing disposal is a distinct possibility.
Lean Tip #532 - Manufacturing companies who want to reduce costs and increase efficiency, should not neglect quality control.
If this area is overlooked, you end up with defects and added waste which will need to be disposed of. More space is required if these products are stored for reworking or repair and therefore means an increase in energy use for heating, cooling and lighting.
If this area is overlooked, you end up with defects and added waste which will need to be disposed of. More space is required if these products are stored for reworking or repair and therefore means an increase in energy use for heating, cooling and lighting.
Lean Tip #533 – Eliminating or reducing waste will maximize product yield, while helping a manufacturing company be more green.
This means less waste will go to landfills and more products made. Additionally, it saves the company money as typically, waste makes up four percent of business turnover.
This means less waste will go to landfills and more products made. Additionally, it saves the company money as typically, waste makes up four percent of business turnover.
Lean Tip #534 - Expand the definition of waste to include not only product and process waste, but also the business consequences of unsustainable practices.
When you expand your thinking, Muda’s list of wastes takes a different form:
• Waste of natural resources
• Waste of human potential
• Waste due to emissions
• Waste from byproducts (reuse potential)
• Terminal waste, that is by-products that have not further usefulness
• Energy waste
• Waste of the unneeded (e.g., packaging)
When sustainability is viewed this way, it isn’t something new that has to be planned from scratch and agonized over. Instead, it can be integrated into existing continuous improvement programs – Lean, or even Six Sigma initiatives.
When you expand your thinking, Muda’s list of wastes takes a different form:
• Waste of natural resources
• Waste of human potential
• Waste due to emissions
• Waste from byproducts (reuse potential)
• Terminal waste, that is by-products that have not further usefulness
• Energy waste
• Waste of the unneeded (e.g., packaging)
When sustainability is viewed this way, it isn’t something new that has to be planned from scratch and agonized over. Instead, it can be integrated into existing continuous improvement programs – Lean, or even Six Sigma initiatives.
Lean Tip #535 - A lean and green supply chain helps manufacturers save money and reduce environmental impact at the same time.
Manufacturers can stay competitive and reduce their environmental footprint at the same time by partnering with the Green Suppliers. By targeting the root causes of wasteful practices along the supply chain you can mutually achieve business and environmental goals.
Manufacturers can stay competitive and reduce their environmental footprint at the same time by partnering with the Green Suppliers. By targeting the root causes of wasteful practices along the supply chain you can mutually achieve business and environmental goals.
Lean Tip #536 – Productivity Tip: Know how you currently spend your time.
The simplest way to do this is to keep a log of what you do each day for a period time. While this may initially feel like a time waster, it is a necessary planning step. Just like you can't budget your money without knowing where you're currently spending it, you can't budget your time without knowing where it's going either. By keeping a log you'll become more aware of stress times and down times, and will be better equipped to plan your time.
The simplest way to do this is to keep a log of what you do each day for a period time. While this may initially feel like a time waster, it is a necessary planning step. Just like you can't budget your money without knowing where you're currently spending it, you can't budget your time without knowing where it's going either. By keeping a log you'll become more aware of stress times and down times, and will be better equipped to plan your time.
Lean Tip #537 – Productivity Tip: Identify your "prime time."
Your "prime time" is your most productive time. For many people that time tends to be in the morning while others find it take a while to get going. By scheduling your most important tasks for the times you're at your best, you'll be able to get them done faster and more effectively.
Your "prime time" is your most productive time. For many people that time tends to be in the morning while others find it take a while to get going. By scheduling your most important tasks for the times you're at your best, you'll be able to get them done faster and more effectively.
Lean Tip #538 – Productivity Tip: Do tomorrow's planning tonight.
Being prepared for the coming day will enable you to get more work done, and be more effective at what you do. As you wind down at the end of the day use this time to create a simple, prioritized to-do list, so you'll be better able to focus on what needs to be done the next day.
Being prepared for the coming day will enable you to get more work done, and be more effective at what you do. As you wind down at the end of the day use this time to create a simple, prioritized to-do list, so you'll be better able to focus on what needs to be done the next day.
Lean Tip #539 – Productivity Tip: Continually ask yourself "Why am I doing what I'm doing right now?"
If you cannot answer this question, you are not being as productive as you could be. Make sure that you are doing something for a specific reason, and simply not wasting your valuable time spinning your wheels.
If you cannot answer this question, you are not being as productive as you could be. Make sure that you are doing something for a specific reason, and simply not wasting your valuable time spinning your wheels.
Lean Tip #540 – Productivity Tip: Handle each piece of paper or e-mail once.
When you have completed a task, either file it away or pass it on to someone else. When doing tasks and making decisions, make the decision and then stick to it. Do not put off making a decision, and don't make vague, wishy-washy decisions. Being more decisive will free you up to move on to other tasks, making you more productive.
When you have completed a task, either file it away or pass it on to someone else. When doing tasks and making decisions, make the decision and then stick to it. Do not put off making a decision, and don't make vague, wishy-washy decisions. Being more decisive will free you up to move on to other tasks, making you more productive.

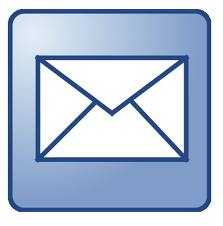




