Like millions of others from around the globe I have been glued to the TV watching the winter Olympics from Sochi. Once again the eyes of the world are on its best and brightest athletes as they attempt to push the human body to new limits, and remind us that our best human qualities — determination, perseverance, innovation, sacrifice, and camaraderie – know no bounds.
As
much as the Olympics represent the pinnacle of the sporting world, they are
also the source of a number of inspiring stories that showcase both the human
spirit and what we can accomplish when we strive to be our best.
To
that end, I’d like to share some important lessons for leaders on how to guide
their organization to succeed and thrive, regardless of the challenges that
stand before them.
Lesson 1: Olympians
know no goal is impossible with the right mindset. If you want to
succeed, don’t lose sight of your goals. Stay unwaveringly motivated. Your
focus determines your results. Focus on the right things.
Lesson 2: When
Olympians suffer an inevitable setback, they don’t let themselves succumb to
doubts.
You can’t compete at the highest levels without inner-confidence. And when you
do get a taste of success, don’t rest on your laurels. You have to pivot, hone
in on the strengths that have carried you so far, and overcome adversity with
perseverance.
Lesson 3: There’s no
substitute for surrounding yourself with the best possible team. With the right
players, there’s no limit to what you can accomplish. Don’t compromise on
talent, and hold yourself to the lofty expectations people will place on you.
Lesson 4: Olympians
break through excuses. Many businesses will face immense challenges on the road
to success. They will also be presented with opportunities to overcome these
challenges. Don’t squander your potential with self-imposed limitations. Don’t
make excuses for why you cannot engage more fully. Capitalizing on your chances
is a matter of being dedicated and sacrificing for the greater good of the business.
Lesson 5: Olympians
never stop learning from mistakes. In business you need to measure everything
so you can analyze how to be more effective, more productive, and more
profitable in the future. What gets measured gets improved. You never settle
for good. You always strive to be great. It’s an attitude of constant
improvement.
Lesson 6: Olympians
give 100% commitment to their goals. You have to give 100% commitment to what it
is you want to achieve. Without a doubt those that are competing have committed
themselves 100%. They don’t expect it to be easy and are ready and willing to
do what it takes.
To
achieve success businesses and leaders within them need to take a long term
view. The reality is there is no shortcut to success. These lessons above show
how we should approach our leadership and guiding the people we lead towards
achieving our shared goals.

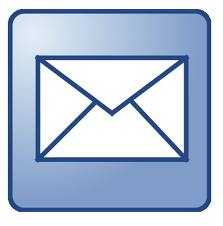




