When I am not at work (as a Quality Manager) and not writing articles for this blog I spend a great deal of time coaching youth ice hockey. This past weekend our season came to an end with the completion of playoffs. As a Lean leader often does I took some time to reflect on this past season.
As
a coach you can’t help but feel a sense of instilling good behaviors in your
players. While you might be teaching specific skills and helping them
understand the strategies of the game I think the opportunities to teach life
lessons are the most important. In my experience I liken this to the way a Lean
Sensei (champion, mentor, teacher) coaches continuous improvement thinking.
They don’t focus on the tools necessarily but rather the approach or method of
problem solving. It is this that provides a valuable foundation of Lean
thinking from which you can address any situation.
As
I looked back over the season I started thinking about the lessons I hope my
players learned. Many of these lessons are the same that I and others try to
instill in the organizations we work with. So in no particular order here are
five lessons that apply to sports and Lean:
1. Never give up. Sports have lots of
highs and lows throughout the game. Perseverance is necessary to turn a bad
situation into a good situation. When your team is behind never give up or you
will be defeated. Lots of teams come from behind to win.
Lean
also needs perseverance to get you through the difficult bumps in the road
along the way to improvement.
2. Practice.
Practice. Practice.
All sports teams practice in order to improve. The key to their practices is to
focus on basic skills for game situations. This high speed sport is much about
reading and reacting so you must practice with intensity if you want to play
with intensity.
In
your organization you may not necessarily call it practice but you certainly
experiment. This experimentation is what prepares us to solve more and more
complex problems.
3. The power of
teamwork. Hockey
is not an individual sport it requires every member of the team to play their
part to win. It also requires everyone to be at their best. Open communication
and chemistry are an essential part of teamwork.
We
all have roles in our organizations but it is the power of teamwork that makes
our endeavors successful. It takes everyone working together on a common goal
to be successful in Lean.
4. The value of hard
work and sacrifice.
Undoubtedly it takes a lot of hard work and sacrifice along the way to get to
the elite levels of the game. But this makes winning so much sweeter in the
end.
Lean
takes lots of hard work as well but it makes wins you get much more
pleasurable. It is this hard work that creates customer value and makes your
organization competitive in the market place.
5. Winning requires a
positive attitude.
There are a lot of things out of our control and adversity is part of the
challenge but how we react is up to us. The right attitude can keep you moving
forward. Never dwell on what you did wrong but what you need to do better for
the next game.
Lean
requires a willingness to try something new to improve our workplace. Fix what
bugs us. Make work easier.
Even
if you’re not a hockey fan like me, I hope you’re able to take some of these
life lessons from ice hockey and apply them to your experiences. I think these
are lessons we can all use especially in a continuous improvement environment.
What do you think?

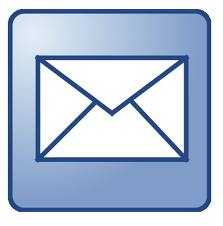




