In the US we are celebrating Columbus Day which recognizes Christopher Columbus who discovered America. This is a good time to talk about the importance of discovery to Lean thinking. Fundamentally, discovery is the act of detecting something new, or something "old" that had been unknown. Discoveries are often made due to questioning.
Thinking is not driven by answers but by questions. To think through or rethink anything, one must ask questions that stimulate our thought.
Questions define tasks, express problems and delineate issues. Answers on the other hand, often signal a full stop in thought. Only when an answer generates a further question does thought continue its life as such.
Thinking is of no use unless it goes somewhere, and again, the questions we ask determine where our thinking goes. Deep questions drive our thought underneath the surface of things; force us to deal with complexity. Questions of purpose force us to define our task. Questions of information force us to look at our sources of information as well as at the quality of our information.
Encourage a questioning culture. Urge everyone to question. Ask why several times to try to get to the root cause of problems. Challenge everyone to think and learn. Because without questioning there can’t be discovery. And without discovery there can’t be improvement.
In the spirit of Columbus Day take some time to discover and learn about your company, your employees, your problems, your processes, and your customers so that you can think Lean improvement.

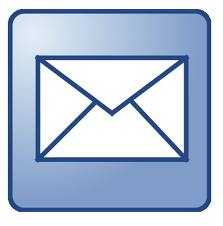




