A common definition of Lean
manufacturing I hear often is paraphrased as “doing more with less”. Honestly,
it is my least favorite. I don’t like it because labels like this rarely capture
the essence of the approach and minimize Lean. It’s origins come from summarizing
Toyota’s results where they we able to do more with less resources.
It is too easy to link this
phrase with firing people. Unfortunately, there are too many people who launch Lean
with the only objective of personnel reduction. Lean manufacturing is not a
head-count reduction system; instead Lean manufacturers understand employees on
the shop floor know their work best. Lean manufacturers don’t want employees to
work harder, or faster – they want employees to work more efficiently. Lean
manufacturing focuses on improving employees, providing more value to the
workforce, and, overall, establishing a dependable and stable workforce.
Lean is about doing more to get
more, knowing that reducing waste is a growth strategy, a way to help the
company be more competitive. Lean is about value — a bigger and more inclusive
concept than mere waste. Lean is a systematic way to learn to see the
inefficiencies in your processes and to solve these opportunities in such a way
to grow the business profitably by adding value the customer will pay for. If
you want to be a successful company you will learn to empower and engage the
entire organization to focus improvement on value-added work from the
customer’s perspective.
Lean is a relentless, continuous,
never ending focus on waste reduction. Lean is all about finding better ways to
do things, so that they require less effort, less time and fewer resources. It
is not about cost reduction – penny-pinching, cutting investment, taking out
people – it is about finding better ways to get work done. Traditional cost
cutting occurs in silos, without regard to who is affected upstream and
downstream. These impacts cannot just negate the initial cost reduction from
the unilateral approach, but exceed them. Lean examines each process, internal
and external, finding and removing the waste, and reducing cost while
maintaining the health of all constituents.
Lean manufacturing means creating
more value for customers with fewer resources while we deliver what the
customer want, with the quality expected and when they need it. Value is
whatever the customers are willing to pay for. Less resources means:
less time, less human effort, less machinery, less materials, less space.
Lean is not easy. It's not easy
to understand. It's not easy to implement. And it's especially not easy to
sustain. But anyone who has embarked on a so-called lean journey already knows
this. Lean, in fact, is hard work and it's a challenge to keep it going.
A label like "doing more with less" just doesn't do justice to Lean and all it is.

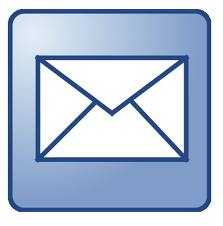





No comments:
Post a Comment