"Back Door" by kpe II via the LAist Featured Photos pool on Flickr
For the experienced identifiying and eliminating waste may not be difficult. For other it may not be easy to find wate when you look at the production line or the warehouse or a process. If you are new to Lean and just starting your journey you may find it even harder to discove the waste right in front of you. As you have heard from many at Toyota it may take hours of just standing and observing people performing an operation before you get a sense of where the waste is. Waste is everywhere, in every operation; it is so common and you are so used to it that it's hard to see. You may have to take the "back-door" approach and look for the opposite of waste: work.
Work is the value-added activity in the operation. It is everything that waste is not. So when you can't see the waste, find the work.
You will need to closely inspect every operation in the entire process. Ask why that operation is happening at that point. Continue to ask why until you have explored the operation in dpeth and are satisfied that you have uncovered the waste and understand the value of the operation or the need to eliminate it. Ask why at least five times of every situation you examine.
Use this approach to your thinking:
1. Look at the three real things:
The factory (functional area)
The facts (data driven thinking)
Work-in-process (material not moving)
2. Ask "what?"
Ask what the operation is about.
3. Ask "why?"
Ask why the operation is necessary.
4. Everything that is not work is waste.
One you have found out what the operation's essential
funtion is, everything in the operation that does not
directly execute that function is waste.
5. Ask "why?" at least five more times to find the root cause.
Ask why at least five times concerning each wasteful part
of the operation. This will lead you to the real waste.
Many who practice Lean Thinking get so focused on waste they forget to find value. Lean is about adding value to the customer first (and respect for people second). While quite effective, eliminating waste is only one countermeasure for contributing more value . So if you have trouble finding the waste that might be right in front of you try coming in the "back door" and look for the value-added work. This is what we are truly after any way. Learning to see often requires us to look with different set glasses

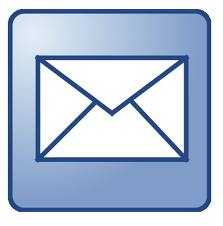





Tim-excellent approach to finding waste. Your five questions provide a good systematic way to find waste. Most of us find it harder to see waste after working in a particular plant for some time-this can help break through that obstacle. Thanks for sharing.
ReplyDeleteChris
How did I miss this post the 1st time on Twitter! I can't agree more look at the value (from the customers point of view)) should be done before looking for waste. Heck, you might even find something that you think is wasteful is of value to a customer. That would be wasteful!
ReplyDeleteActually, my first thought went to an old product development practice that is still pinned up on my wall, SCAMPER:
What can you Substitute?
What can you Combine?
What can you Adapt?
What can you Modify or Magnify?
Can you Put to other uses?
What can you Eliminate or reduce?
What can you Reverse/Rearrange?
Using this approach has helped me find value in many things. If you cannot find value after this, guess what - it probably is waste!
Joe, Thanks for sharing the acrynom SCAMPER. I hadn't seen it that way before. Glad you liked the post.
ReplyDeleteTim