Rules create structure in our systems. Without rules there would be in chaos. Lean rules provide the guidance needed to implement improvement, explaining the “why” behind lean tools and the Six Sigma methodology. Lean rules also help develop new solutions to problems. For everyone in an organization, these rules help structure activities, connect customers and suppliers, specify and simplify flow paths, and bring improvement through experimentation at the right level.
In their paper Decoding the DNA of the Toyota Production System, Harvard Business Review, 1999, S. Spear and H.K. Brown boiled down the essence of the Toyota method to these Lean 4 Rules-In-Use:
Rule 1: All work shall be highly specified as to content, sequence, timing, and outcome.
Specify in advance the exact Content, Sequence, Timing, and Outcome of work.
- Content (what is being done?)
- Sequence (in what order?)
- Timing (how long should it take?)
- Outcome (what clearly defined measurable results are expected?)
Rule 2: Every customer-supplier connection must be direct, and there must be an unambiguous yes-or-no way to send requests and receive responses.
Interaction between Humans, Materials, and Information should be Clear, Direct, and Binary. No ambiguity.
Create a workplace that is:
Self-ordering
Self-improving
Self-regulating
Self-explaining
What is supposed to happen, does happen, on time, every time.
Rule 3: The pathway for every product and service must be simple and direct.
Organize for uninterrupted flow with simple, direct paths for work flow. The pathway should not be subject to interpretation on a case-by-case basis. Build in self-diagnostics so when a path is not being followed, it should be obvious and immediately correctable without too much time passing or outside intervention required.
Rule 4: Continuously Improve
Develop leaders who can apply the scientific method to improve anything. Allow improvement to come from the source by those doing the work - as close to the problem as possible. Respond directly to any problem that arises with clear helping/coaching chains. Whenever possible, start as an experiment supported by a coach.
Toyota developed this set of principles, Rules-in-Use, as the building blocks of a production system. They allow organizations to gain maximum efficiency so everyone can contribute at or near his or her potential. When the parts (activities, connections, and pathways) come together the whole is much, much greater than the sum of the parts.

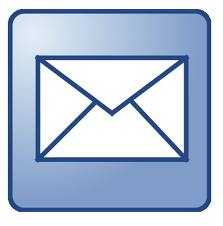





No comments:
Post a Comment